Best Practices for Extending the Lifespan of Your Pump Motor
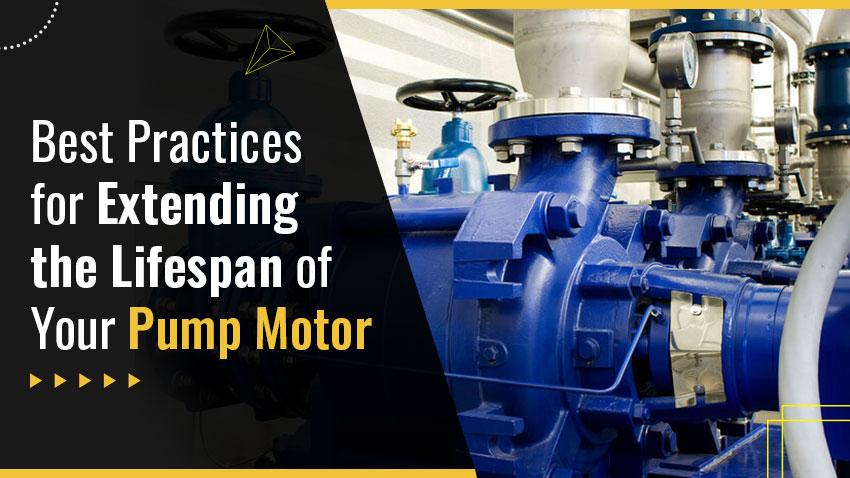
Pumps and Your Business
Pumps come in many shapes and sizes and play a critical role in a wide variety of industrial applications. From chemical processing plants to water treatment facilities, pumps ensure the seamless movement of liquids from one area to another. They heavily contribute to the functionality of industrial-grade machinery and hold a special place in many pieces of infrastructure.
Your company may utilize centrifugal, positive displacement, or reciprocating pumps to meet your industrial needs. But regardless of the pump type, proper maintenance and care can go a long way toward extending its longevity.
In this blog, we’ll explore some best practices to help you get the most out of your industrial pump motors. If you hope to maximize efficiency and minimize costly downtime, the following information is for you.
10 Best Practices to Extend the Life of Your Pump
Pump motor repair can lead to significant expenses, so it makes sense to adopt strategies that put as little strain on industrial pumps as possible. Let’s examine a few easy ways to accomplish this:
1. Regular Maintenance
Regular maintenance is the cornerstone of pump longevity. Establish a routine maintenance schedule that includes inspection, cleaning, and component checks. This can help identify potential issues before they escalate, preventing costly repairs and downtime.
2. Monitoring Shaft Wear
The pump shaft is a critical component, and wear can lead to performance issues. Regularly monitor the shaft for signs of wear and address any issues promptly. Pump motor repair services, such as motor rewinding, can be employed to rectify problems in the shaft and ensure optimal functioning.
3. Ensuring Proper Seals
Seals play a crucial role in preventing leaks and maintaining pump efficiency. Regularly inspect and replace seals as needed. Properly sealed pumps not only operate more efficiently but also avoid contamination of the pumped fluid.
4. Monitor Vibrations
Excessive vibrations can indicate misalignment or wear in pump components. Implement vibration monitoring systems to detect irregularities early on. Addressing vibrations promptly can prevent further damage and extend the life of your pump.
5. Ensure Proper Alignment
Misalignment can lead to increased wear and tear on pump components. Regularly check and adjust the alignment of the pump and motor to ensure they are correctly positioned. This simple step can significantly enhance the longevity of the equipment.
6. Monitor Lubrication Levels
Adequate lubrication is essential for reducing friction and preventing premature wear. Regularly check lubrication levels and follow manufacturer recommendations for the type and frequency of lubrication. This is a fundamental aspect of pump motor repair and maintenance.
7. Operate the Pump at Its BEP (Best Efficiency Point
Pumps are designed to operate most efficiently at specific flow rates and pressures. Running the pump at or near its Best Efficiency Point (BEP) enhances performance and reduces wear. Straying too far from the BEP can lead to inefficiencies and premature wear.
8. Never Run a Pump Dry
Running a pump without an adequate fluid supply can cause overheating and damage. Always ensure that the pump is properly primed and has a continuous flow of fluid to avoid unnecessary stress on components. This practice is crucial in preventing the need for extensive pump motor repair.
9. Understand the Material Being Pumped
Different fluids have varying levels of viscosity, corrosiveness, and abrasiveness. Understanding the material being pumped helps in selecting the right pump materials and components. This knowledge ensures that your pump is equipped to handle specific challenges, reducing the risk of damage.
10. Check Surrounding Piping
The condition of the piping connected to the pump can impact its performance. Inspect the surrounding piping for leaks, corrosion, or any irregularities. Addressing issues with the piping system can contribute to the overall health and longevity of the pump.
The Importance of Regular Preventative Pump Maintenance
Now that we’re more familiar with some methods of preventing early wear and tear on your pump, let’s look into why performing regular maintenance matters and what it can do to improve your business functionality:
1. Improves Pump Efficiency
Over time, factors such as wear and tear, misalignments, or inadequate lubrication can impede performance and lower efficiency. By addressing these issues through routine checks and maintenance, pumps can operate closer to their design specifications, ensuring maximum productivity in fluid transfer processes.
2. Extends the Overall Lifespan
Pumps are significant investments for any industrial operation, and maximizing their lifespan is crucial for cost-effectiveness. Regular maintenance helps mitigate the effects of wear and tear. A proactive approach can significantly extend the overall lifespan of your pump, postponing the need for premature replacements.
3. Minimizes Downtime
Downtime in industrial settings can have far-reaching consequences, affecting production schedules and causing major financial losses. Regular preventative maintenance minimizes the risk of unexpected pump failures. By identifying and addressing potential issues early on, scheduled maintenance activities can be planned to minimize disruption to operations, ensuring a smoother workflow.
4. Reduces Additional Repair Costs
Neglecting regular maintenance can lead to small issues that escalate into major problems, resulting in expensive repairs. Routine checks and timely interventions help catch problems in their infancy, preventing the need for extensive pump motor repair. Take Care of Your Pumps and Industrial Equipment with AES Whether you’re interested in restoring pumps or seeking help for your electronic, hydraulic, or mechanical equipment woes, AES has you covered with a comprehensive array of repair services to tackle any need. Our experienced technicians have years of experience in a wide variety of industries and can bring you effective answers to any problem. Need quick mechanical repairs? We have you covered. How about printer and kiosk maintenance? We do that, too. Our experts can quickly get you up and running, reducing downtime and production costs. Or perhaps you need some insight on how to keep your machinery working at its best. No matter the need, you can trust the technicians at AES. Contact us today at 866-386-1001 to learn more about the many services we provide and what we can do for you, because nobody delivers like AES.
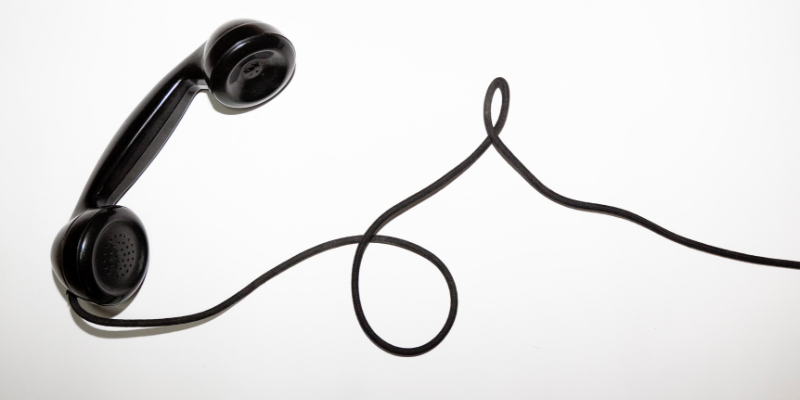
