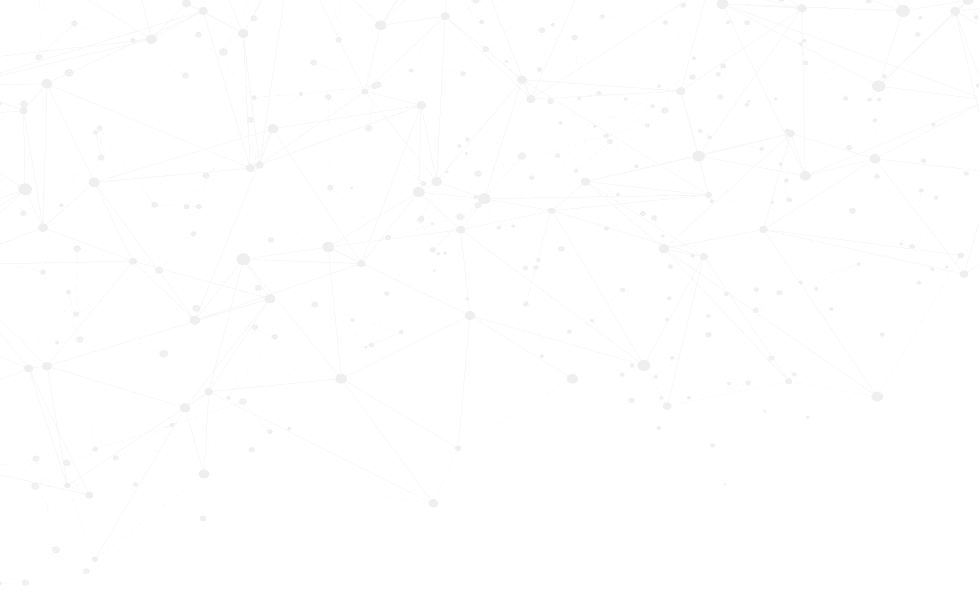
Brake Coil Repair & Rewinding
If your business relies upon industrial motors, drives, and servos to get things moving, motor brakes and brake motors are also necessary parts of the equation. But if your brakes aren’t braking, you may need some brake coil service! AES has a complete machine shop for brake coil repairs, brake coil rewinding, brake rebuilding, and whatever else you may need.
Quickly Search for an Mechanical Equipment you are looking for:
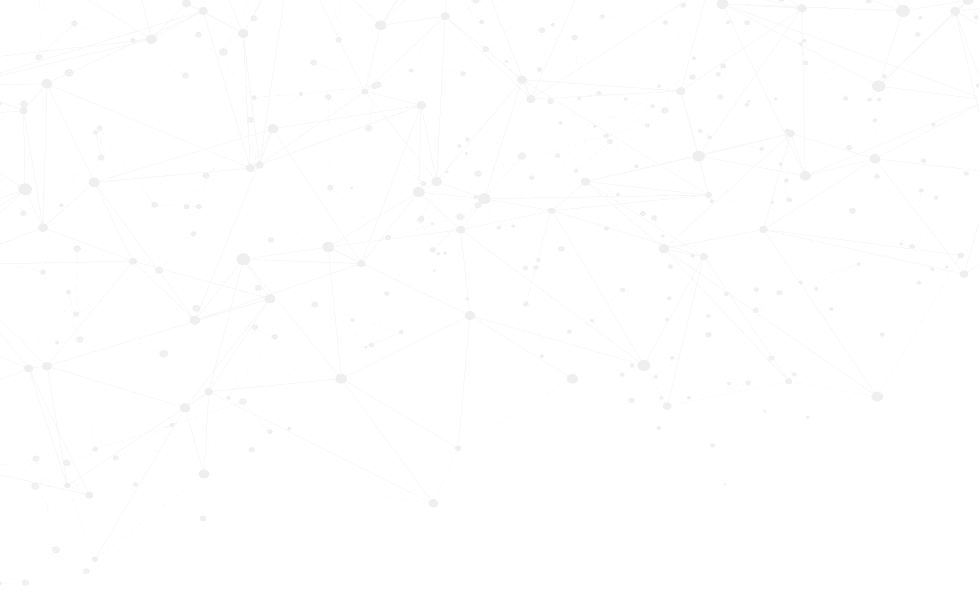
Request a Quote
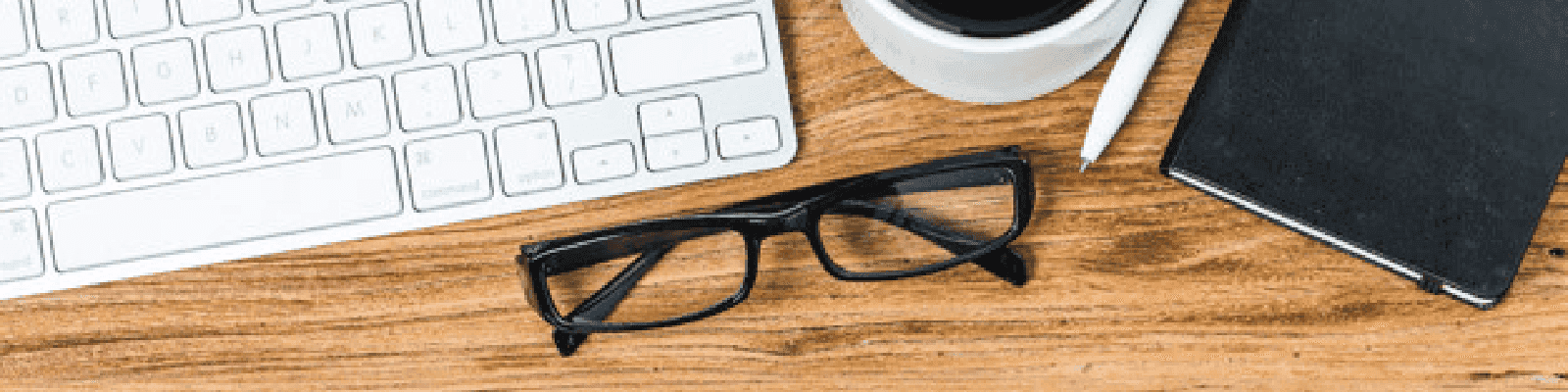
Get in Touch
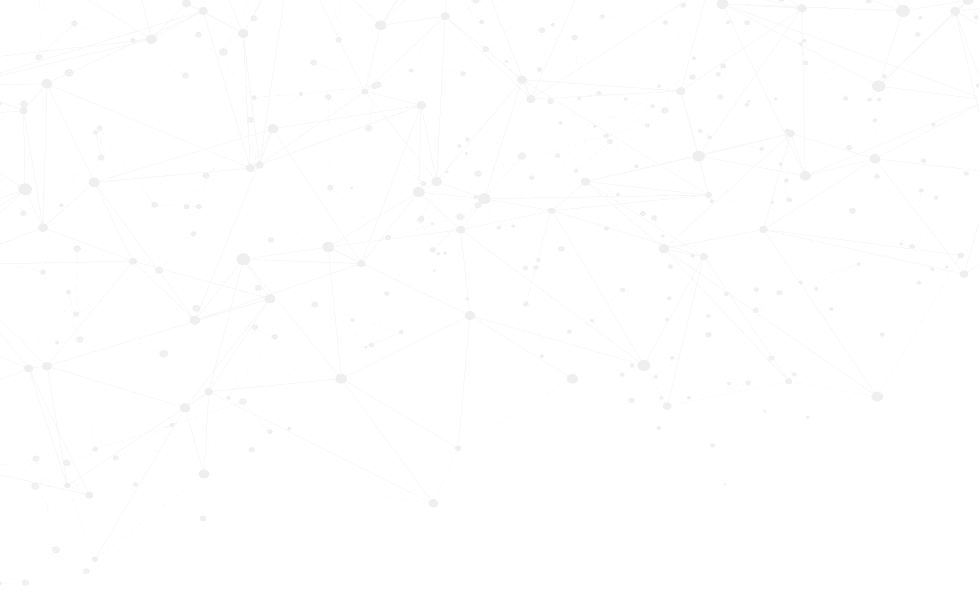
Get started with our simple, proven AES Repair Process
Once we have received your item for repair, we will receive the item in our system.
1Our quoting specialists will evaluate your item and determine the parts and labor necessary to complete the repair.
2Following your approval, we will get to work on your repair. One of our repair technicians will troubleshoot the problem(s) with the item.
3To ensure the highest level of quality throughout the repair process, we comply with ISO 9001:2015 Certified QMS standards, and an ESD program.
4Once the repair is complete, we safely package your item and prepare the item for delivery or shipment.
5Our Partners and Brands We Repair
All product names, trademarks, brands and logos used on this site are the property of their respective owners. The depiction, description or sale of products featuring these names, trademarks, brands and logos is for identification purposes only and is not intended to indicate any affiliation with or authorization by any rights holder.
What’s a Brake Coil, and What Does It Do?
Motors and brakes work in close tandem to create both the force needed to drive industrial equipment, as well as the stopping power to hold it in an exact specified position. In industrial motor brake applications, either springs or magnets are typically utilized to clamp the brake friction surfaces together for stopping power. Whenever the brake needs to be released, an electrical current is passed through the electromagnetically-wound brake coil to produce a field which is able to overcome the spring or magnet pressure, thus retracting the brake mechanism.
Electromagnetic brake devices of this nature are used in all sorts of applications, including those which rely upon electric motors, drives, servos. Electromagnetic brakes can be found on everything from heavy-duty vehicles, to public transportation applications, to power tools, manufacturing equipment, production equipment, robotics, mills, crane and hoist systems, fail-safe brakes, and other holding or E-stop applications.
What Can Lead to Brake Coil Failure?
Being able to set a heavy piece of machinery is important, but being able to stop it on a dime when needed is equally crucial. Brake coils are very effective at producing needed stopping power at high torques, but over time certain issues can crop up with your brake coils, too. What are some leading causes of brake coil failure?
Supply voltage issues
If the provided line voltage exceeds 110% of the coil’s rating, that could cause the coil to fail. Other voltage-related problems could include trying to power a DC coil with AC input (or vice-versa), or experiencing excessive voltage drops during inrush conditions.
Wiring issues
Depending upon how your unit was designed and installed, the lead wires could interfere with plunger pull-in or other moving components. Your coil lead wire can be shorted if not properly grounded, as well. Sometimes your coil may simply need to be rewound with more protective wire sleeving.
Application and temperature issues
If your machinery cycle rate exceeds the coil rating, that can result in problems for your brake coil system. Ambient temperatures which rise above your coil’s insulation rating can also lead to coil breakdown and failure.
Worn solenoid or other parts
Over time, your shading coils can become broken, your torque spring can become overtightened, the lever arm-pinion assembly may need replacing, or there could be excessive solenoid wear at the mating surface. Some of these parts could also have been installed or mounted improperly to begin with, as well.
Excessive air gap
If the air gap in your brake coil system is too large, the magnetism generated may still not be enough to engage (or release) the braking system. Once an air gap is set correctly, in most cases, it should never require readjusting. But if the air gap wasn’t set right to begin with, this is an issue that will have to be addressed in order to get your brake coil working correctly.
Proven Brake Coil Service Process with AES
Got a brake coil that needs adjusting, repairing, or rewinding? You’re in good hands with the AES team; our machine and motor repair team is fully-equipped to serve your needs! We’ve developed a proven process for repairing, rewinding, and restoring all sorts of wound coil systems, including brake coils.
Send It to Us
Pack your brake coil unit with foam, bubble wrap, or similar protective material, and just send it! Also, it would be helpful if you could try to describe any particular symptoms or issues you’ve been experiencing with your equipment. But if all you know is that it isn’t working right, that’s fine – our team can still figure it out for you!
Shipping Instructions
Ship your equipment to AES at 101 Technology Lane, Mount Airy, NC 27030, with your name, company name, phone number, email, mailing address, and any other relevant contact information. We’ll get the ball rolling with our initial analysis, and we’ll let you know what we find with our troubleshooting & analysis.
Equipment Check-in, Evaluation, & Repair Quote
Once your equipment arrives at our facility, we’ll check it in and assign unique tracking IDs for every piece of equipment. We’ll go through our troubleshooting and evaluation process, and will thoroughly analyze your brake coil. Once we finish that, we’ll generate a complete repair quote detailing exactly what we’ll need to do in order to fully restore your equipment to like-new condition.
Personalized Follow-Up
Your individual Customer Service Representative will connect with you personally; at AES, we just believe the personal, individual touch is best. We’ll let you know that we’ve received your equipment and reviewed it, and we’ll give you all the details of what we were able to discover, including repair recommendations and cost quotes.
Let’s Do It!
After you approve our repair service quote, we’ll put your brake coil right on our repair team’s schedule! We follow a very thorough process for handling brake coil breakdown, repair, rewinding, and restoration. Once everything is reassembled, we’ll conduct some full-load tests to make sure everything is working properly. Once our service is complete, we’ll carefully package your items for a safe return, and then we’ll promptly ship everything back to you.
Why You Should Entrust AES with Your Brake Coil Repair Services
Let’s face it, replacing an industrial motor brake system can get expensive. But replacement isn’t your only option; AES also offers effective repair and rewinding solutions, which are just as effective, if not more effective. We can offer you a better, more affordable repair solution for your brake coil!
Quality Repair Work
At AES, quality is one of our cornerstone values. Our commitment is to provide you with the best possible quality of repair services for every piece of equipment you entrust into our care. We’ve successfully repaired a ton of wound coils for all sorts of applications, including brake coils. We, at AES, can take care of your equipment repair needs, too.
Quick Turnaround Time
Obviously, in an ideal world, your repairs could be completed instantly! But breaking down a brake coil, servicing it, and rewinding it will require a certain amount of time, attention, and effort. But don’t worry – our trained & skilled team has all the knowledge, tools, and experience to be able to get it done for you correctly, as quickly as possible! Our standard turnaround time is 8-10 business days for most projects, but you can also opt to place a RUSH on your order if that’s what you need. We’ll work hard to meet your timetable!
Experienced Repair Technicians
Brake coils and other wound coils aren’t just something we do on the side; at AES, we have specially-trained technicians who focus exclusively on just these sorts of projects! Plus, our team collectively possesses decades of combined experience, so you can trust that we know how to take care of your equipment. We provide ongoing training opportunities for our team too, so we’ll always be in a great position to serve your needs, both now and in the future.
An Effective AND Cost-Effective Solution
Repair and service solutions done right are almost always a better solution when it comes to industrial equipment! We can service your brake coil for LESS, and we can restore it to like-new (or better) condition, too! Our clients appreciate the way AES comes alongside to meet their equipment service needs, while also saving them a good bit of time, money, and needless headaches.
Industry’s Best Warranty!
You don’t want to miss this point, either. Every repair provider will assure you that they do good work, but not all providers will go the extra step to actually put their money where their mouth is. At AES, we’re proud to stand behind our work, which is why we offer a 24-Month Limited Warranty for ALL REPAIRS! If a problem should arise within that time frame, which is deemed to be a repair workmanship issue, we’ll provide a follow-up repair service for you at NO charge! We’re a repair partner you can trust!
Connect with AES for Your Brake Coil Rewinding & Repair Service Needs
Ready to get your brake coil working properly, so your equipment can both start AND stop when needed? We can take care of that for you, and more; AES has you covered! Reach out today at (866) 386-1001, and let us provide you with your perfect repair solution! We’re standing by to help!