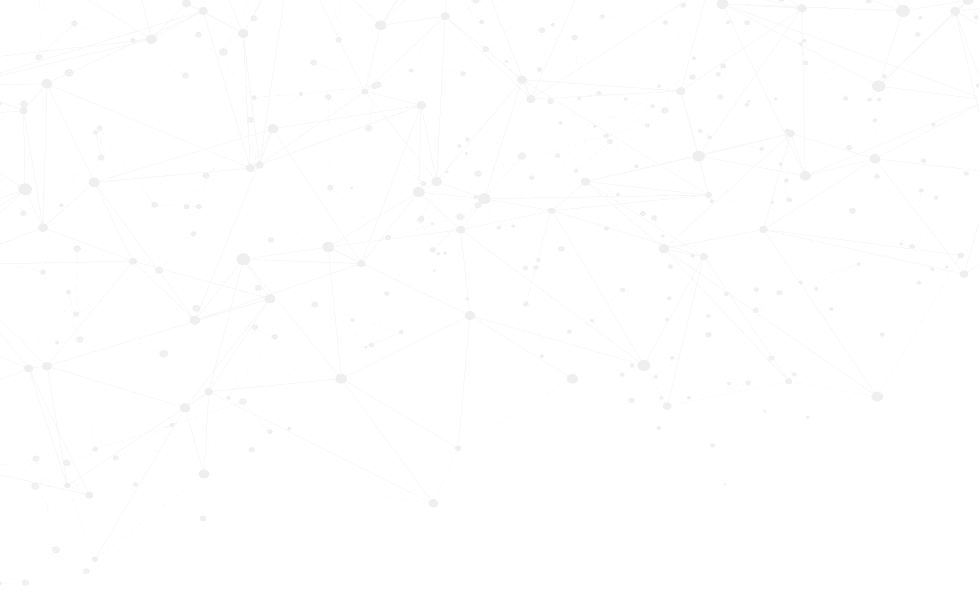
Control Box Repair Services
Being able to use technology in a safe and effective manner includes your ability to control it. For heavy-duty equipment, many of these electronic controls are located within the control box. If you’re currently experiencing an equipment problem, your control box may be the culprit. Time to call the service experts at AES! If you’ve got a control box issue, the AES team can help!

Quickly Search for an Electronic Equipment you are looking for:
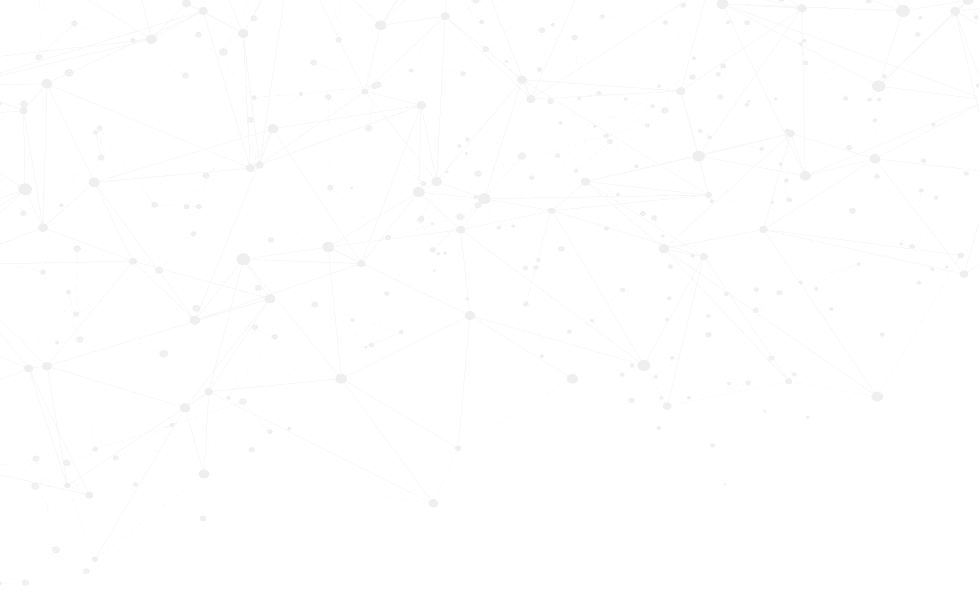
Request a Quote
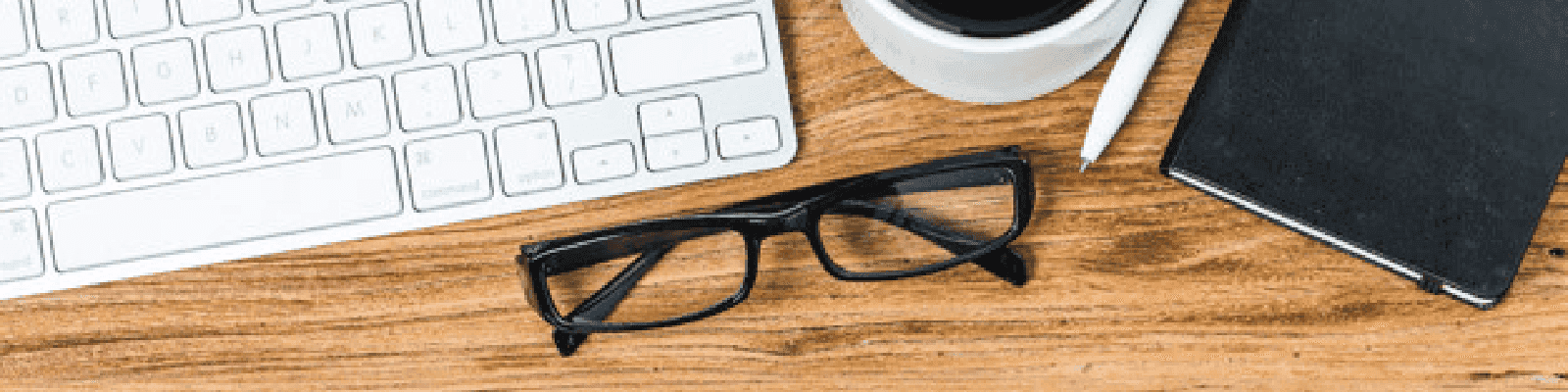
Get in Touch
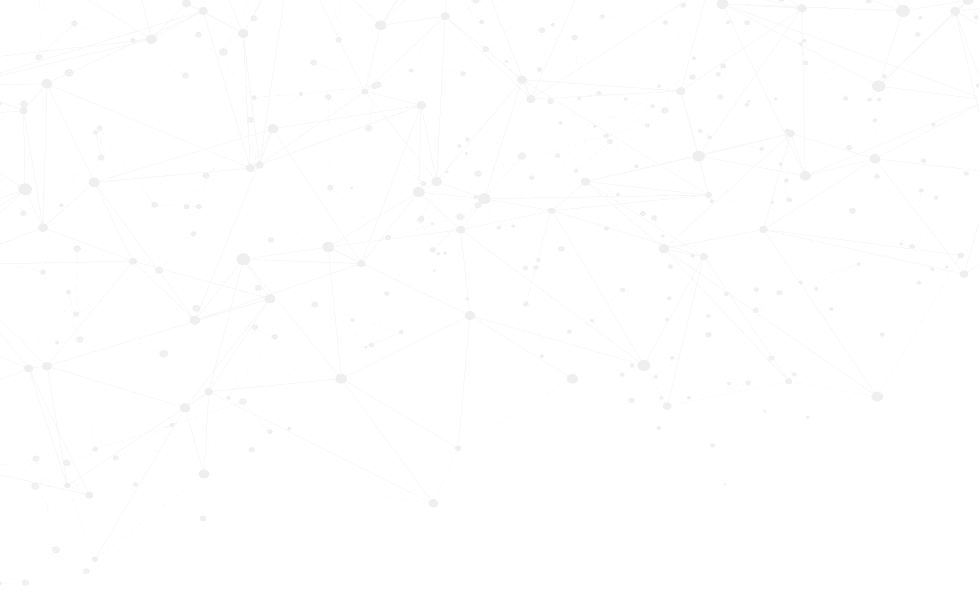
Get started with our simple, proven AES Repair Process
Once we have received your item for repair, we will receive the item in our system.
1Our quoting specialists will evaluate your item and determine the parts and labor necessary to complete the repair.
2Following your approval, we will get to work on your repair. One of our repair technicians will troubleshoot the problem(s) with the item.
3To ensure the highest level of quality throughout the repair process, we comply with ISO 9001:2015 Certified QMS standards, and an ESD program.
4Once the repair is complete, we safely package your item and prepare the item for delivery or shipment.
5Our Partners and Brands We Repair
All product names, trademarks, brands and logos used on this site are the property of their respective owners. The depiction, description or sale of products featuring these names, trademarks, brands and logos is for identification purposes only and is not intended to indicate any affiliation with or authorization by any rights holder.
What’s a Control Box?
A control box is essentially utilized as a means for controlling connected heavy-duty equipment. Control boxes are utilized across a variety of industries, including medical applications, manufacturing, production, and other applications. Depending upon your particular needs and required functionality, customized software can be written to manage the various movements and processes of your equipment, whether in an individual, synchronized, or simultaneous manner.
Control Box Basics
Control boxes are used to govern a wide assortment of equipment, so sometimes it can be hard to define what’s included in each respective control box design. Nevertheless, there are common features found in most any control box. A control box typically comprises various instruments, including switches, knobs, buttons, and sliders. These instruments are directly connected to the equipment they are designed to govern, and they allow operators to start, stop, or adjust various equipment functions. A control box is essentially the physical interface which allows an operator to both control a particular piece of equipment, and also monitor how it’s performing in the process. To that end, control boxes are also able to receive data from various sensors, which is then used to help verify that the machinery is functioning correctly and in line with your expectations. All the controls are typically enclosed within the box in a secure manner to prevent any accidental contact or unauthorized access to the controls.
Troubleshooting a Control Box
Unless you’re familiar with the inner workings of a control box and are also comfortable testing various aspects of electrical equipment, specific troubleshooting procedures are best left to a trained professional – like those you’ll find at AES! Here are some tests we can perform to thoroughly diagnose your control box:
Measure voltage at the pressure switch
The voltage at L1 and L2 of your pressure switch should be +/- 10% of the motor rating. Excessive voltage drop can come from loose connections, bad contacts, ground faults, or an inadequate power supply. Any relay chatter can also be caused by low voltage or ground faults.
Measure voltage at the control panel
Same as the voltage at the pressure switch, your control panel voltage reading should be +/- 10% of the motor rating.
Check the overloads
Testing the overloads entails checking every solder point with an ohmmeter. We’re looking for any readings less than 0.5. A zero reading indicates that the overloads are tripped; in that case, we’ll reset the overloads and then retest.
Check the run and start capacitors
We remove the capacitors, and then attach the ohmmeter leads to the terminals. The reading on the ohmmeter should initially fall, and then climb towards 1 if the capacitor is good.
Potential (voltage) relay coil test
We remove the relay, and attach the ohmmeter leads to connections #2 & #5. A good coil should measure between 4.5 and 7.0.
Potential (voltage) relay contact test
Next, we attach the leads to connections #1 & #2. A correct reading for a good contact should register zero ohms.
Line contactor coil test
We remove the line contactor, and then attach the ohmmeter leads to the contactor coil terminals. A correct meter reading for a good coil should register between 1.8 and 14.0.
Line contactor test
Attach the ohmmeter leads to either L1 & T1 or L2 & T2. Once the contacts are manually closed, a correct meter reading should display zero ohms.
Why Choose AES for Your Control Box Repair Services?
Since our founding in 1992, AES has established a solid track record of providing successful repairs for our customers and clients, including control boxes. We help to keep your essential equipment running, so you can keep doing what you do best! Here are some things that really set AES apart:
Faster Turnaround
A quality control box repair will take time to conduct properly, but the AES team is well-positioned to be able to get it done faster, too! We offer a quick standard turnaround time of 8-10 business days for most repairs, but we can also put a RUSH of 1-3 business days on your project, should you so designate when placing your order.
Quality Repair Work
Some might say the way we do things at AES is old-fashioned, but we just believe in doing things the right way! We provide an exceptional quality of service for every single repair we provide for every client, every single time. We’ve successfully repaired control boxes, along with every other imaginable type of electronic equipment for our customers and clients, and we know what it takes to get your equipment working again properly, too!
A Team of Real Professionals
We know we can serve your needs well at AES. How can we be so sure? Our team of repair technicians owns a collective ton of relevant experience – we’ve worked on pretty much everything that’s out there! We’re also intentional about providing regular ongoing training for our team, so we can ensure that we’ll be ready to serve your needs in the future, too.
A More Cost-Effective Solution
Why pay to replace an expensive control box, when all you really may need is some timely maintenance service and repair work? AES can take care of your needs, and we’ll get your control box back up and running properly. By choosing to partner with AES, you’ll also save time, money, and prevent many needless headaches.
The Best Repair Warranty!
Here’s one more convincing reason to partner with AES. Naturally, everyone says they do good repair work, but sometimes that’s no more than just a bunch of talks. At AES, we stand behind every service we provide by offering you a 24-Month Limited Warranty! Essentially, what that means is that if a problem should arise within the warranty period, which is deemed to be a repair workmanship issue, AES will provide follow-up repair service for you at NO additional cost! How’s that for impressive service?
Connect with AES for Your Control Box Repair Services
Ready to get your control boxes back online, and working the way they should? We can take care of that; AES has you covered! Reach out today at (866) 386-1001, and let’s get the ball rolling! We’re here to help!