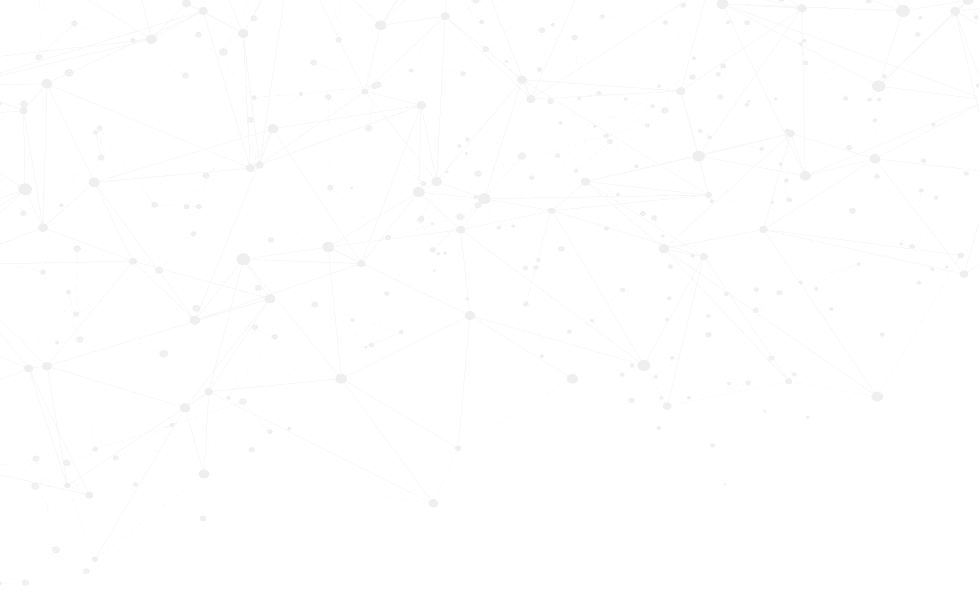
Hoist Motor Repair
If lifting, moving, and relocating heavy items or equipment is a requirement for your business, the chances are good that you depend upon a hoist or crane mechanism. But if your hoist has stopped hoisting, then your productivity can also grind to a halt! AES has a complete machine shop for repairing hoist assemblies and the motors which drive them. We can restore the lift to your hoist!
Quickly Search for an Mechanical Equipment you are looking for:
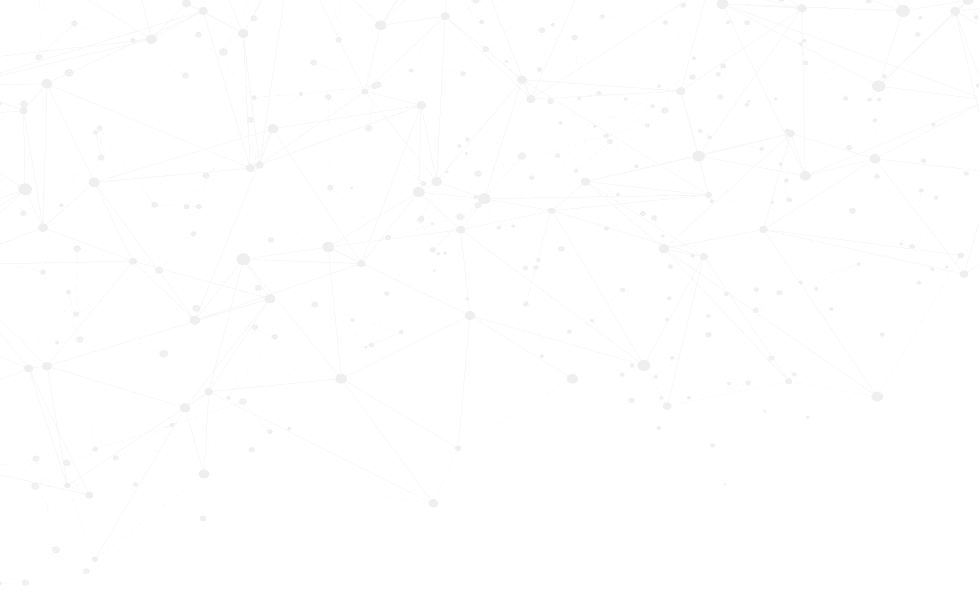
Request a Quote
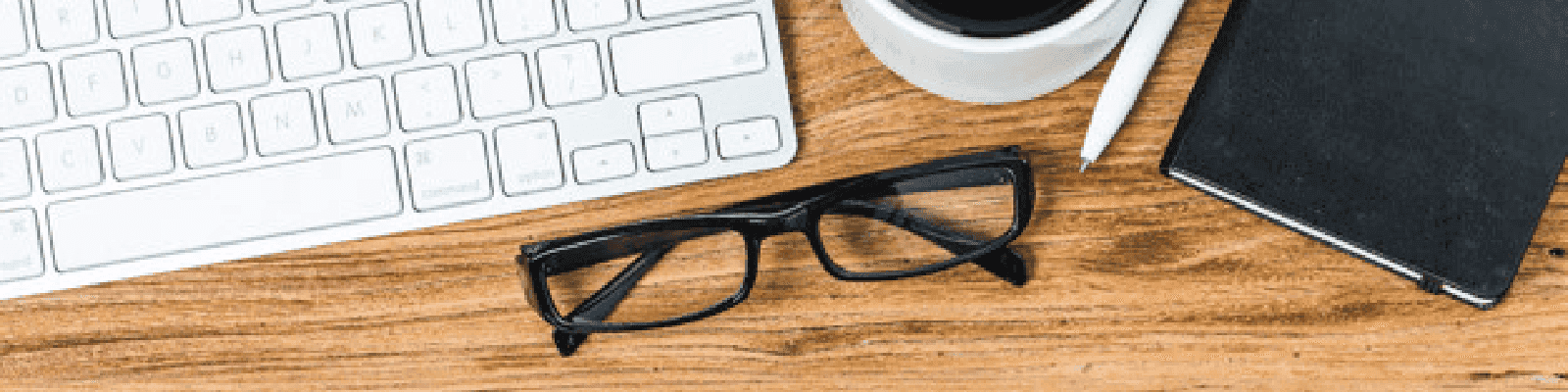
Get in Touch
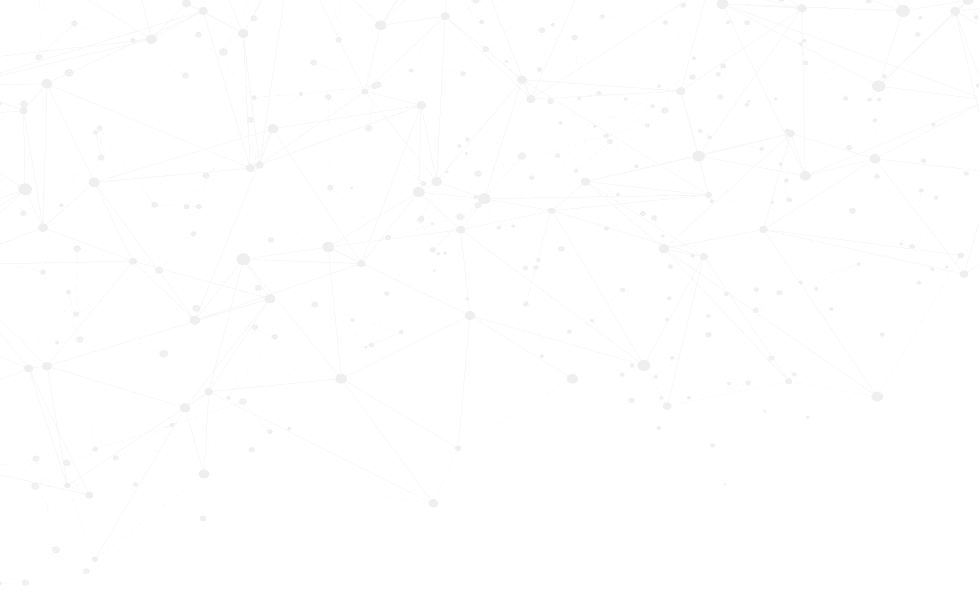
Get started with our simple, proven AES Repair Process
Once we have received your item for repair, we will receive the item in our system.
1Our quoting specialists will evaluate your item and determine the parts and labor necessary to complete the repair.
2Following your approval, we will get to work on your repair. One of our repair technicians will troubleshoot the problem(s) with the item.
3To ensure the highest level of quality throughout the repair process, we comply with ISO 9001:2015 Certified QMS standards, and an ESD program.
4Once the repair is complete, we safely package your item and prepare the item for delivery or shipment.
5Our Partners and Brands We Repair
All product names, trademarks, brands and logos used on this site are the property of their respective owners. The depiction, description or sale of products featuring these names, trademarks, brands and logos is for identification purposes only and is not intended to indicate any affiliation with or authorization by any rights holder.
What’s a Hoist Motor, and How Does It Work?
The term “hoist” is commonly used to describe any sort of equipment which is designed to lift and lower a load. Most hoists operate on a simple pulley principle, gaining leverage through the use of a drum or lift-wheel around which the cable, wire rope, or chain wraps. The most common type of overhead hoist used in industrial environments depends upon a special electric motor for providing the needed lifting and lowering force for heavy loads. In most cases, the hoist couples to its load by means of a lifting hook mounted to the end of the cable or chain. In addition to electric chain hoists and electric wire rope hoists, there are also many other sorts of winches, levers, trolleys, and hand chain hoists which can be used for specific applications.
What Can Lead to Hoist System Failures?
Because a hoist is a connected system comprised of many moving parts, there are several areas where things can potentially break down or result in a problem. Here are a few of the more common issues we see with hoists and electric hoist motors at AES:
Overload hardware stresses
Hooks and rigging components are designed for specific types and ranges of loads. Asking your hoist to do more than it was designed to be able to handle can result in cracked, bent, stretched, or broken hardware.
Wire rope or cable problems
One of the most common issues that can arise is damage to the cable itself. These metal wires can become corroded, worn, or frayed over time, even with normal usage. Wires can also become crimped or compressed, and can even be cut in some circumstances.
Misalignment issues
A hoist system designed for heavy loads must be kept in proper alignment. Even a slight misalignment can put undue stress and strain on your equipment, and can result in some major problems. If you hear any unusual noises, see any wheels or moving parts which aren’t operating properly, or notice your electric motor to be struggling, straining, or working harder than it should, stop operations immediately and give the AES team a call at (866) 386-1001.
Electric motor problems or electrical system issues
Sometimes your electric hoist motor just comes to the point in its service life where it simply needs to be rewound in order to continue functioning properly. Our team is an expert at rewinding all sorts of electric motors, servos, and drives. Other threats to your electrical system include poor contacts, contaminant infiltration, corrosion, overheating, and faulty pendants or other control devices.
Proven Hoist Repair Process with AES
Got a hoist motor or hoist system that needs adjusting, repairing, or rebuilding? The AES team can take care of your needs; our machine and motor technicians are completely equipped and fully trained for servicing, rewinding, and restoring hoist motors and hoist systems of all types and brands.
Send It to AES
Pack your hoist motor and any related hoist system components with foam, bubble wrap, or appropriate protective material, and send your items to us! Got a large hoist which requires its own shipping container? We can work with those, too. And if you’ve noticed any specific symptoms or issues with your equipment, be sure to let us know about those too. But if you’re not trained in troubleshooting hoists, and just know that yours isn’t working right – that’s fine too! Let our team troubleshoot it for you!
Shipping Instructions
Ship your equipment to AES at 101 Technology Lane, Mount Airy, NC 27030, with your name, company name, phone number, email, mailing address, and any other relevant contact information. We’ll take it from there, and will promptly get the ball rolling on restoring your hoist to full functionality.
Equipment Check-in, Troubleshooting, & Repair Quote
Once your equipment comes to us, we’ll check it in and assign it a unique tracking ID. We’ll then go right into our troubleshooting and evaluation process, and will thoroughly check out your hoist motor and/or hoist system. Once that’s complete, we’ll generate a detailed repair quote describing exactly what needs to happen in order to restore your equipment to like-new condition.
Personalized Follow-Up
Your individually-assigned Customer Service Representative will connect with you personally; at AES, we just believe the personal, individual touch is best. We’ll let you know what we discover after analyzing your equipment, including any repair or replacement recommendations and service quotes.
Let’s Make It Happen!
Once you approve the quote for service, we’ll get your hoist right on our repair schedule! We follow a very thorough process in terms of hoist breakdown, repair, hoist motor rewinding, and restoration service. Once everything is reassembled, we’ll conduct full-load testing to make sure everything is working smoothly. Once everything is finished, we’ll carefully package your items for a safe return, and then we’ll promptly ship it all back to you.
Why You Should Entrust AES with Your Hoist Motor Repair Services
The fact of the matter is that replacing your hoist motor, or your entire hoist system, is an expensive proposition. But with AES, our repair and rewinding solutions are just as effective, if not more effective. We can provide you a better, more affordable repair solution for your hoist!
Quality Repairs
At AES, quality is at the heart of everything we do. We’re committed to providing you with the best possible quality of repair services for any and every piece of equipment you entrust into our care. We’ve successfully repaired all sorts of hoists and hoist motors for all sorts of applications, and we can take care of your equipment repair needs, too.
Fast Turnaround Time
Obviously, you’d love to have your hoist repair completed immediately! But breaking down a hoist motor, servicing it, rewinding it, and restoring it will require some time and attention. But don’t worry – that doesn’t mean our trained & skilled team can’t get it done for you quickly, too! Our standard turnaround time is 8-10 business days for most projects, but you can also opt to place a RUSH on your order if that’s what your timetable dictates.
Experienced Technician Team
Electric hoist motors and related items aren’t something we just do on the side at AES. In fact, we have a dedicated motor and machine service team that focuses exclusively on this type of equipment! We’re incredibly experienced in doing this type of work, so you can trust that we know what we’re doing. But experience isn’t our only teacher; we also provide ongoing training opportunities for our team, to make sure we’ll always be in the best position to serve your needs, both now and going forward.
An Effective, Cost-Effective Solution
Repair and service solutions done right are almost always a better solution when it comes to industrial equipment like hoists and hoist motors. We can service your hoist for LESS, plus we can restore it to like-new (or better) condition! Our clients appreciate how AES comes alongside to meet their equipment service needs, while also saving them a significant amount of time & money, and also preventing many needless headaches.
Industry’s Best Warranty!
Don’t skip by this point, either. Every repair provider will naturally promise to do good work, but not all providers stand behind their promises the same way. At AES, we’re so confident in the quality of our work that we offer a 24-Month Limited Warranty for ALL REPAIRS! If a problem should arise within that time frame, which is deemed to be a repair workmanship issue, we’ll provide a follow-up repair service for you at NO cost! Now, that’s a service you can trust!
Connect with AES for Your Hoist Repair & Restoration
Ready to get your hoist lifting and lowering properly, so you can get all your loads where they need to be? We can take care of that for you, and more; AES has your needs covered! Reach out today at (866) 386-1001, and let us provide you with a perfect repair solution! We’re standing by to help!