Having issues with your hydraulic pumps, motors, valves, hydraulic cylinders, or air cylinders? You could just pay to replace them, or you can let AES save you some $$$ by providing effective and timely repairs to your equipment! AES offers complete hydraulic equipment repair services, including load testing and unit remanufacturing for practically every major hydraulic brand.
Our Offerings in Hydraulic Repairs
If your business relies upon hydraulic industrial equipment for any essential applications, then you’re also depending upon your hydraulic cylinders to function properly. But whenever there’s an issue with a hydraulic cylinder, your hydraulic equipment could be sidelined as well. The hydraulic service pros at AES can provide a solution! Our team of highly trained experts can diagnose and resolve these issues easily. Trust our experienced professionals; they provide complete hydraulic equipment repair services and can take care of your other repair needs, too!

If your business utilizes much in the way of industrial equipment, the chances are good that hydraulics are a part of your machinery. But if there’s an issue with your hydraulic pump, your hydraulic equipment could be rendered essentially useless. At AES, our team of highly trained experts specializes in repairing hydraulic pumps. They have the skills, knowledge, and expertise to easily diagnose and address any issues. You can trust our experienced professionals to restore your hydraulic pump to its best condition, ensuring a reliable performance that last!
The hydraulic equipment you rely upon to help make your business go won’t get very far without an effective hydraulic motor powering it. If there happens to be an issue with your hydraulic motor, your industrial equipment may be rendered effectively useless. But no need to worry, AES has got your back. Our highly trained team of experts can diagnose and fix any problems your hydraulic motor may be experiencing. Trust their experience, skills, and knowledge to restore your hydraulic motor to its optimal condition.
Hydraulic pumps help produce needed pressure, but hydraulic valves are also important as they help to direct fluids to and from your hydraulic cylinders. If there’s a problem with any part of your hydraulic system, the valves are really one of the first things you should check. The AES team offers comprehensive valve repair and replacement services for all sorts of hydraulic equipment applications. With years of experience in hydraulic repair services, our team at AES addresses the root cause of the issue and restores hydraulic valves to their best condition. You can rely on our expertise and leave the repairing process to us without any worries.
Hydraulic Equipment


Industries We Serve in Hydraulics!
Our Partners and Brands We Repair
All product names, trademarks, brands and logos used on this site are the property of their respective owners. The depiction, description or sale of products featuring these names, trademarks, brands and logos is for identification purposes only and is not intended to indicate any affiliation with or authorization by any rights holder.
Hydraulic Machine Repair for All Components of Your System
The AES trained team of experts can provide repairs for virtually any hydraulic component, including pumps, motors, valves, cylinders, servo drives, and more. Whether you’re a small business, a large-scale enterprise, or a nonprofit organization, we can take care of your needs. Here are just some of our hydraulic repair specialties:
Hydraulic Pumps: Including pistons, vanes, and gears A busted piston pump is all it takes to take your entire industrial hydraulic system offline. Don’t get stressed with trying to figure out how to replace the entire unit; let the AES team fix your hydraulic pump and get your system running again for less!
Hydraulic Cylinders: These powerful tools use the pressure of the liquid to perform mechanical work, and they allow a little applied force to go a long way! But hydraulic cylinders are also susceptible to wear and tear over time, and our team is trained to help you by providing hydraulic cylinder testing and repair services.
Hydraulic Motors: Including pistons, vanes, and gears While a hydraulic system takes advantage of leveraging pressurized liquids to help accomplish work, it still needs a motor to make everything go. And just like motors in other types of systems, a hydraulic motor can eventually wear out, break down, or just require some specialized service.
Hydraulic Valves: Including flow control, pressure control, and directional Valves are part of nearly every hydraulic system. In hydraulic applications, a valve acts as a sort of switch, directing where the fluid should go in order to operate all the key devices in the system, including hydraulic motors, pumps, and actuators. Some common issues that often arise with hydraulic valves include seal issues, hardware issues, faulty spring assemblies, or spools in need of service.
The Comprehensive Approach to Hydraulic Repair Services at AES
At AES, we understand that any effective hydraulic component repair first requires a thorough understanding of each particular hydraulic system as a whole. When you entrust your hydraulic or pneumatic equipment repair to us, you can rest easy knowing that we provide comprehensive service from a complete systems approach:
Disassembly: Sometimes the best way to figure out what’s needed with a complex system is to start by taking it apart. Our trained hydraulic technicians follow a systematic disassembly process which allows us not just to understand your particular system, but also to assess the condition of each individual component.
Cleaning & Inspection: Cleaning and inspection are essential steps to make sure all hardware, seals, and moving parts are in good working order. We’ll make a thorough examination of every system component, so we can look for any telltale signs of issues that might need addressing.
Testing & Repair of Onboard Electronics: After the component inspection and cleaning are complete, our technicians next move on to conducting tests of all onboard electronics. At AES, we are EXPERTS at all things related to industrial electronics repair, so we know well both how to diagnose and repair any issues we may find.
Elimination of Piston & Shaft Scoring: Scoring and pitting are common issues that can crop up in pistons and shafts with time and use. Our team has all the needed tools and experience for honing, polishing, and even refinishing piston or shaft components, so they’ll work like new again!
Removal of Contaminants: Sometimes surfaces can accumulate contaminants like oil, grease, or corrosive cleaners. If left unaddressed, these contaminants can degrade your hydraulic system and eventually even lead to a total system breakdown. By taking care of these contaminant issues, our team can really help to extend the working life of your hydraulic equipment.
Cylinder Machine Work & Shaft Review: Next, we’ll check on the machinery of the cylinders and shafts themselves. Some components may require some simple reconditioning, and at this stage, we’ll also fix any broken shafts and replace any other essential items which require it.
Check & Assess All Fittings: We make sure to check every fitting to make sure it meets spec for important parameters, including pressure tolerance, psi loads, and GPM flow. We also take diameter and angle tolerances into account for each respective fitting. Fitting checks like these ensure that your hydraulic system is able to operate at maximum levels of both performance and efficiency.
Resurfacing of Every Contact Point: Resurfacing of contact points is another critical step of the process. Removal of scratches and abrasions helps to reduce friction, and ultimately improves the efficiency of your hydraulic equipment.
Replacement of Seals & Bearings: The last step in our repair process includes replacing the bearings and seals. Worn-out bearings and leaky seals are two of the most common causes of hydraulic equipment failure. By allowing the AES team to perform this preventative measure, you’re really investing in the long-term reliable performance of your hydraulic system!
Final Testing & Quality Checks: Before we sign off on your hydraulic system, once everything is reassembled, we’ll conduct a series of final tests and quality checks to make sure everything is operating as it should. Our systematic approach is thorough and uncompromising, and we ensure that your hydraulic equipment is in tip-top shape before we ever put it back into your hands.
Why Choose AES? Learn More About the AES Difference!
You may be able to find other companies who also claim to offer hydraulic equipment repair service, but they simply won’t take care of you with the same level of careful workmanship and personalized customer service you’ll receive from AES! We’ll take care of your repair needs, and we’ll also take care of you in the process:
Comprehensive Service: AES is truly a “one-stop-shop” for all your industrial equipment repair needs. We specialize in providing hydraulic repair, but we also have dedicated teams of technicians who specialize in providing other important services as well. And in addition to our teams of technicians, we also employ an in-house team of engineers to help us best diagnose your problem, and even rebuild your entire system if necessary. If it needs fixing, we can do it!
Dedication to Quality: AES believes in doing the job right for you the first time, and every time! After seeing the quality of our work along with the many ways we can come alongside to help, most of the customers choose to become long-term clients of AES. We thrive on unique challenges, and we’re committed to hang in there and continue to work on the problem until we’re able to provide you with the absolute best solution for your needs.
Faster Turnaround Time: A quality hydraulic equipment repair takes time to do right, especially with our extensive systems repair approach. But our team isn’t just competent. Thanks to our many years of experience, we’re also very efficient at what we do. In fact, we’re able to get your job completed faster than our competitors. And if time is really of the essence, then no one can meet your needs better than AES! We offer a quick, standard turnaround time of 8-10 business days for most projects, but we can also provide you with a RUSH turnaround time of 1-3 business days, if that’s what your timeline dictates!
Trained, Experienced, & Ready to Serve: Our team knows what we’re doing! Many of our repair technicians possess 20-30 years of experience (or more!) in their respective fields. But we’re still not satisfied, either. We know that investing in regular training opportunities for our team is a sound investment, both in our individual employees and in the capability of AES to continue to serve you well in the future.
FREE Evaluations & Competitive Pricing: AES is happy to offer FREE evaluations and quotes for each and every repair service. We’ll diagnose your problem and explain exactly what your repair solution will involve, before you ever place your order with us. We’re also committed to completing your project with prices that are always competitive and fair. And our personal standard of workmanship is second to none!
Personalized Customer Service: Some other repair companies can make you feel like “just a number,” but that’s NOT what we’re about at AES. In a word, every customer relationship matters to us. We don’t just see you as just a customer or a client; we see you as a real partner. At AES, we assign you to an individual account manager and account specialist. That way, we can take care of your needs and take care of you at the same time.
Affordable Solutions: Why pay to replace an expensive piece of hydraulic equipment, when our team can repair and/or refurbish it for LESS? One of the things our clients like best about AES is the way we come alongside to meet your hydraulic repair needs, while also saving you some money!
Industry’s Best Warranty! : And here’s another game-changer when it comes to choosing AES. We believe in the quality of our services and workmanship so much that we provide a 24-Month Limited Warranty for ALL REPAIRS! If a problem arises within that time frame, which is related to the workmanship of AES, we’ll provide any needed follow-up service at no additional cost!
Trust AES for All Your Hydraulic Repair & Service Needs
AES has been providing quality electronic and industrial mechanical repair since our beginning back in 1992, and we continue to do so today, including our complete slate of hydraulic equipment repairs and services. We’ve also expanded to include the sale of both new and used industrial equipment components from thousands of respected supply vendors, in order to better meet the needs of our many customers. You can trust AES with your hydraulic equipment repairs, and you can also entrust your other surplus industrial equipment needs to us as well.
Ready to get the conversation started? Just fill out our Request a Quote form, shoot us an email at sales@aesintl.com, or give us a call at (866) 386-1001. We’ll do our best to provide what you need, when you need it, and we’ll do so with the best customer service in the business! Got an industrial equipment problem that needs fixing? AES is here to help!
Latest Articles & Videos on Hydraulic Repairs
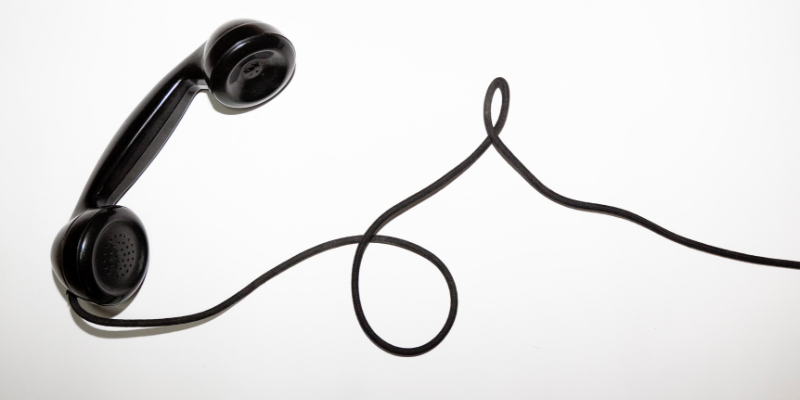
