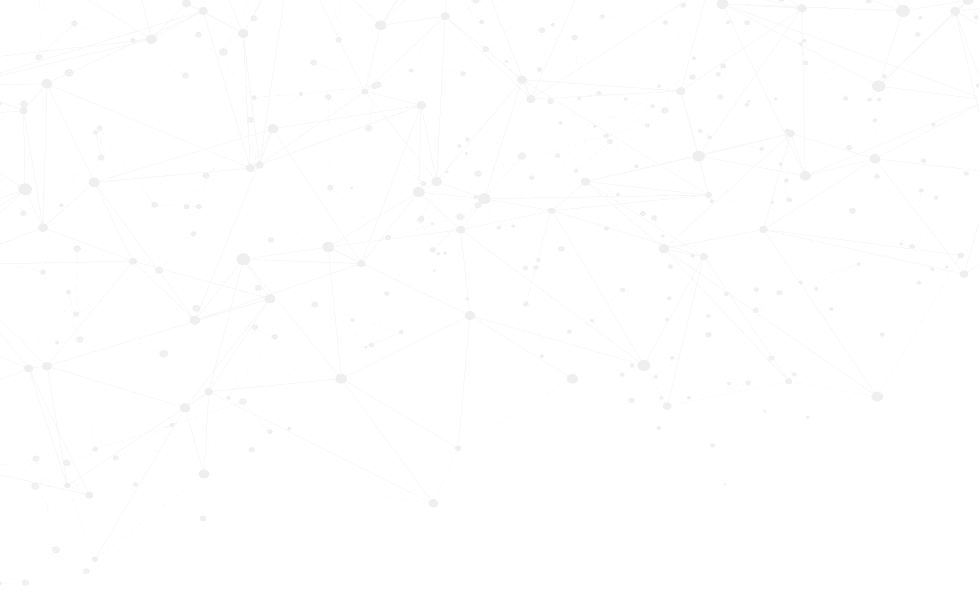
Hydraulic Valve Repair
Hydraulic pumps help produce needed pressure, but hydraulic valves are also important as they help to direct fluids to and from your hydraulic cylinders. If there’s a problem with any part of your hydraulic system, the valves are really one of the first things you should check. The AES team offers comprehensive valve repair and replacement services for all sorts of hydraulic equipment applications. With years of experience in hydraulic repair services, our team at AES addresses the root cause of the issue and restores hydraulic valves to their best condition. You can rely on our expertise and leave the repairing process to us without any worries.
Quickly Search for an Hydraulic Equipment you are looking for:
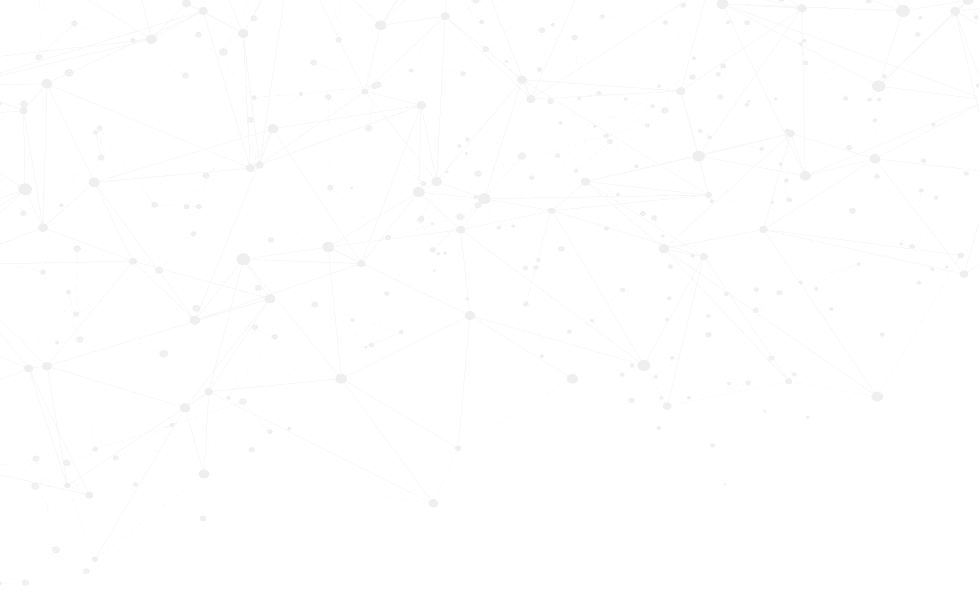
Request a Quote
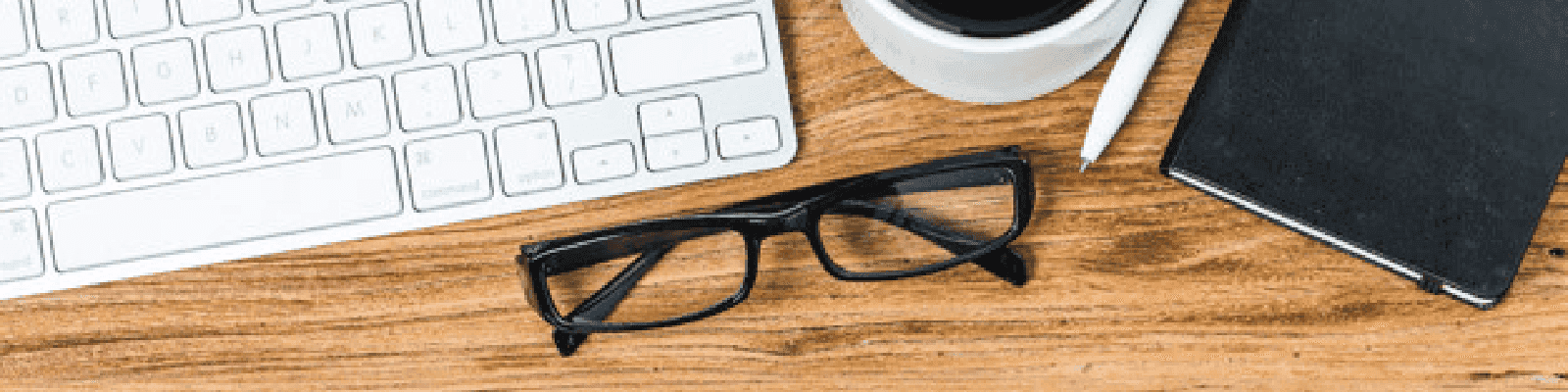
Get in Touch
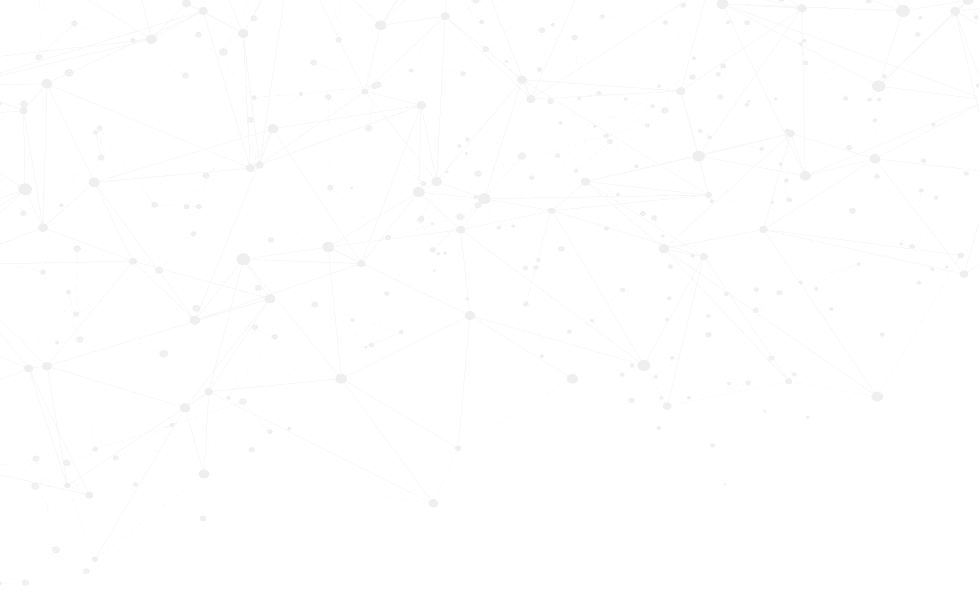
Get started with our simple, proven AES Repair Process
Once we have received your item for repair, we will receive the item in our system.
1Our quoting specialists will evaluate your item and determine the parts and labor necessary to complete the repair.
2Following your approval, we will get to work on your repair. One of our repair technicians will troubleshoot the problem(s) with the item.
3To ensure the highest level of quality throughout the repair process, we comply with ISO 9001:2015 Certified QMS standards, and an ESD program.
4Once the repair is complete, we safely package your item and prepare the item for delivery or shipment.
5Our Partners and Brands We Repair
All product names, trademarks, brands and logos used on this site are the property of their respective owners. The depiction, description or sale of products featuring these names, trademarks, brands and logos is for identification purposes only and is not intended to indicate any affiliation with or authorization by any rights holder.
What Are Hydraulic Valves, and How Do They Work?
Valves are an important component of essentially every kind of hydraulic application. Hydraulic valves serve the important function of directing and regulating the flow of vital fluids to all key areas of the system, including hydraulic pumps, actuators, cylinders, and motors. They can be controlled either manually or automatically, and can be activated by physical, mechanical, electric, hydraulic, or pneumatic means. In industrial applications, hydraulic valves are typically engineered to be able to withstand extremely high levels of fluid pressure; many hydraulic systems involve pressures reaching 3000 psi or greater!
There are many types of industrial valve styles and designs, many of which are common to other types of valve applications as well. These include butterfly valves, ball valves, bypass relief valves, check valves, needle valves, diaphragm valves, plug valves, diverter valves, regulating valves, and more. In terms of broader categories, hydraulic valves are typically characterized in one of three groups: pressure control valves, flow control valves, and directional control valves.
What Are Some Symptoms of Hydraulic Valve Failure?
Some common issues that often lead to hydraulic valve problems include faulty seals, hardware issues, faulty spring assemblies, or spools that are in need of service. But short of checking each and every individual valve within your hydraulic system (assuming you even know how to do that), how do you know whether a valve issue may even be the problem? Great question! Here are a few likely signs of hydraulic valve failure:
System won’t reach the correct pressure
If your system won’t reach the required pressure, this could be a sign of valve failure. In some cases, this could be fixable – it could simply mean that your valve (or valves) was calibrated to the wrong set pressure and is releasing early. If that doesn’t fix the issue, and it seems like every other part of your system is functioning normally, then your pressure relief valves may simply need to be changed.
System is operating above the prescribed maximum pressure
When (or if) your system builds up above maximum recommended pressure for safety, relief valves should open to let off some built-up pressure. But if your system is above pressure and your valves aren’t being released, this often means there’s a problem with one or more of the valves themselves. As mentioned above, this could just be a calibration issue, or it could mean that your valves have simply failed and require replacing.
Valve with a visual leak, or a pressure valve that displays no pressure at all
In the first two cases, it may not always be easy to see the problem at the valve source itself. But if one or more of your valves are visibly leaking, there can be no doubt where the issue lies. In other cases, you may not be able to see the actual leak, but you can still know it’s there whenever a pressure valve displays no pressure at all. In cases like this, one of three things has likely happened: either the valve has a loose fit, the spring is broken, or the balance hole has become plugged. In either case, prompt service is required in order to restore your hydraulic system to its proper operating condition.
Hydraulic Valve Repair, Maintenance, & Replacement with AES
Got some hydraulic valves which seem to be sticking or simply aren’t engaging properly? Don’t let those valves slow down your productivity – entrust the job to the AES team! We’ve serviced a ton of hydraulic valves & equipment, and we can take care of any items you send our way!
Send Your Hydraulic Equipment to AES
Pack your hydraulic equipment with foam, bubble wrap, or appropriate protective material, and just send it on to AES! If you’re also able to describe any specific issues you’ve been noticing, that could help us as well. But if all you know is that your hydraulic equipment isn’t working right and you think the hydraulic valves may be the issue, send it on anyway! Our team will be happy to troubleshoot & diagnose it for you, and then we can provide whatever repairs or service may be needed.
Shipping Instructions
Ship your equipment to AES at 101 Technology Lane, Mount Airy, NC 27030, with your name, company name, phone number, email, mailing address, and any other relevant contact information. Our team will take it from there, and we’ll be glad to get to work on your hydraulic valve issues.
Equipment Check-in, Troubleshooting, & Repair Quote
Once we receive your hydraulic equipment, we’ll check it in and give it a unique tracking ID. Then we’ll move into our troubleshooting and evaluation phase, which includes breaking your components down, inspecting the valves, and making our expert assessment. We’ll then be ready to share a repair & service quote which describes what we’ll need to do to get your equipment working as good as new.
Personalized Follow-Up
Your individually-assigned Customer Service Representative will connect with you personally; at AES, we just believe the individual, personal touch is best. We’ll let you know what we discover after our expert analysis, including any specific repair, service, or valve replacement recommendations.
Let’s Get Your Hydraulic Valves Working Again!
Once you officially approve our repair quote, we’ll immediately place your hydraulic equipment on our team’s service schedule. We follow a proven, time-tested process for hydraulic equipment breakdown, valve service, restoration, and rebuilding. Once we get everything reassembled, we’ll put your equipment through a series of full-load testing to make sure everything’s working properly. After some final quality assurance measures, we’ll carefully package your items for a safe return, and then promptly ship it all back to you.
Why You Should Entrust AES with Your Hydraulic Valve Service
Replacing a valve-operated hydraulic component or complete system can become rather expensive. The good news is that component, or system replacement may not be needed, especially if you can partner with an effective hydraulic equipment service partner. The AES team is here to offer more effective, more affordable repair solutions!
Quality Repairs & Service
At AES, providing quality service is really the cornerstone of our business. Our commitment to you is to deliver the absolute best quality of repair, service, and maintenance for every item you decide to send our way. We’ve successfully repaired a wide range of hydraulic valve-based items, as well as pneumatic and electronic components. Our team can absolutely take care of your particular equipment repair needs, too.
Quick Turnaround
When asked what your ideal repair turnaround time is, most likely, your answer would be NOW. We understand! But the reality is that a quality valve repair does require a certain amount of time to complete with accuracy and precision. Thankfully, the AES team has all the knowledge, tools, and experience needed to do the job right, and we can get it done fast, too! Our standard turnaround time for most projects is 8-10 business days, but you can also choose to put a RUSH on your order, if your turnaround timetable is particularly tight. We’ll work hard to meet your schedule!
Experienced, Trained Professionals
At AES, we have specially-trained technicians who focus on repairing hydraulic and pneumatic equipment, including pumps, motors, cylinders, and valves. We collectively possess decades of combined on-the-job experience, so we really do know what we’re doing! We also provide our team with ongoing training opportunities, to make sure we’ll always be in a great position to serve your needs.
A Solution That’s Both Effective And Cost-Effective
Why pay to just replace an expensive piece of equipment, when quality repairs and service may be all that are really needed? We can service your industrial hydraulic equipment for LESS, plus we’ll return your equipment to you in like-new (or better) condition. AES is known for effectively meeting our clients’ equipment repair needs, and they also really like the way we’re able to save them time, money, and needless headaches!
Industry-Leading Warranty!
Please don’t miss this point about AES, either. Most any repair providers will try and assure you that they do good work, but most repair providers won’t back their service with a warranty of much significance. At AES, we’re proud to stand behind everything we do by providing a 24-Month Limited Warranty for ALL REPAIRS! Should a problem arise during that time frame, which is deemed to be related to our workmanship, we’ll provide a follow-up repair service for you at NO additional cost! You really won’t find a better warranty in the industrial equipment repair industry!
Connect with AES for Your Hydraulic Valve Repair Services
Ready to get all your hydraulic valves working properly, so your hydraulic equipment can continue putting in the work that you need? We can take care of that for you, and more; AES has you covered! Connect with one of our friendly team members today at (866) 386-1001, and allow us to provide you with your perfect repair solution! We’re standing by to help!