Manufacturing Equipment Repair Services
Are you in the business of manufacturing or production? If so, you almost certainly rely upon a number of types of specialized devices and equipment every day. But what happens if one of your pieces of equipment breaks down, or simply isn’t performing the way you need it to? AES has been serving the needs of commercial & industrial manufacturing clients for decades, and we can provide you best equipment repair solution!
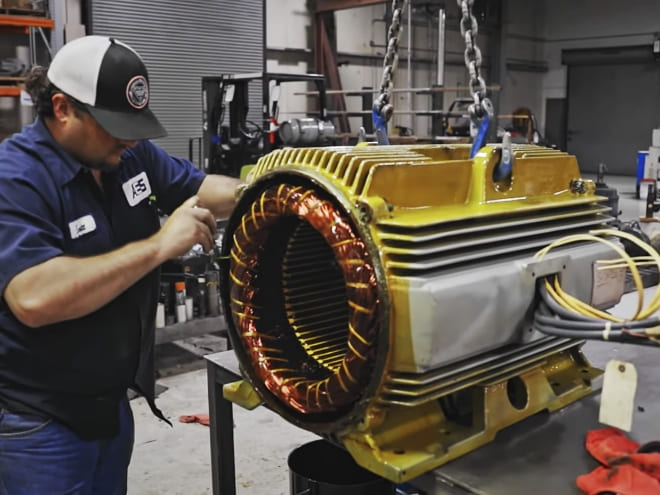
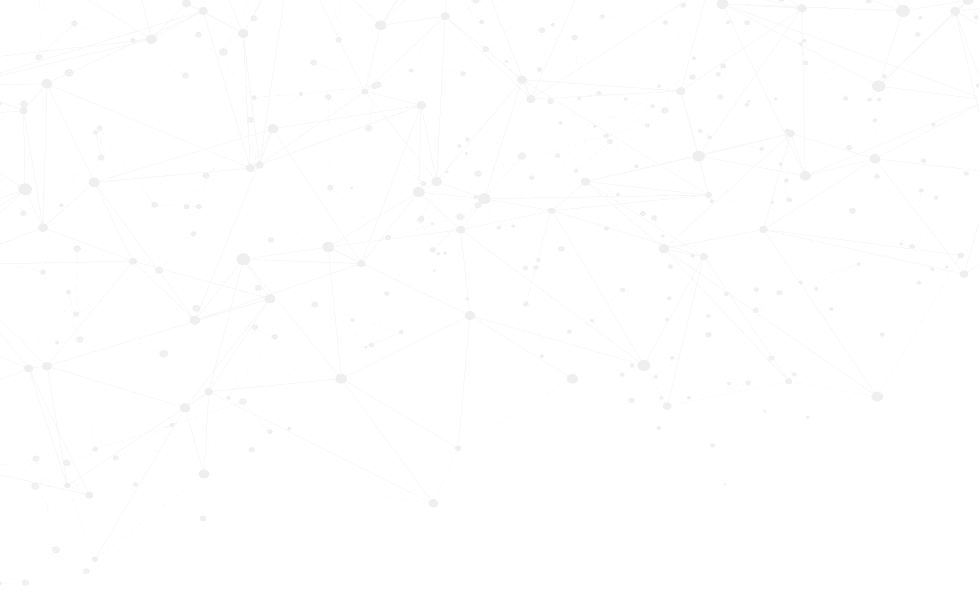
See how AES Repairs helping Medical Industry to Advance
Get started with our simple, proven AES Repair Process
Once we have received your item for repair, we will receive the item in our system.
1Our quoting specialists will evaluate your item and determine the parts and labor necessary to complete the repair.
2Following your approval, we will get to work on your repair. One of our repair technicians will troubleshoot the problem(s) with the item.
3To ensure the highest level of quality throughout the repair process, we comply with ISO 9001:2015 Certified QMS standards, and an ESD program.
4Once the repair is complete, we safely package your item and prepare the item for delivery or shipment.
5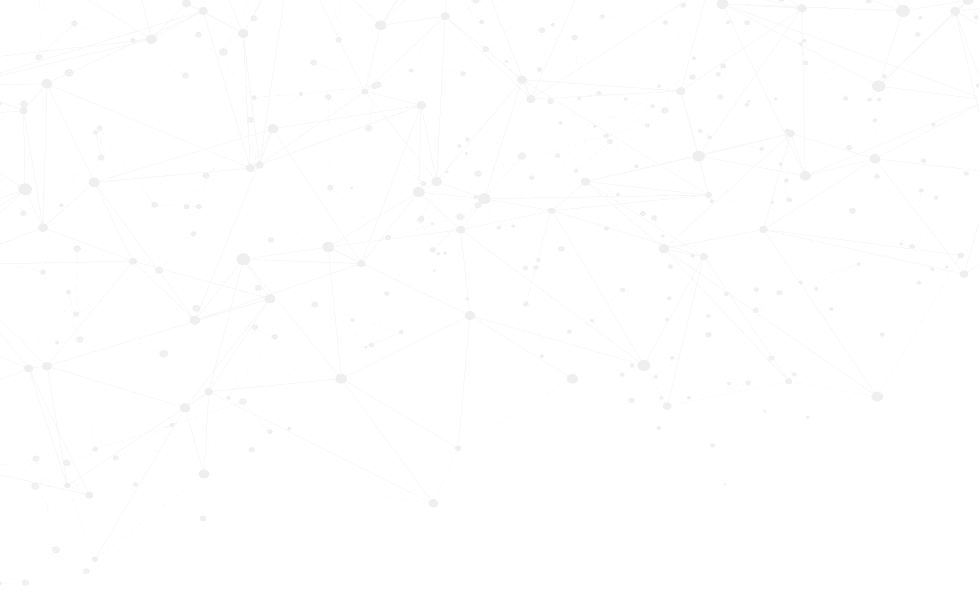
Explore more Industries We Serve!
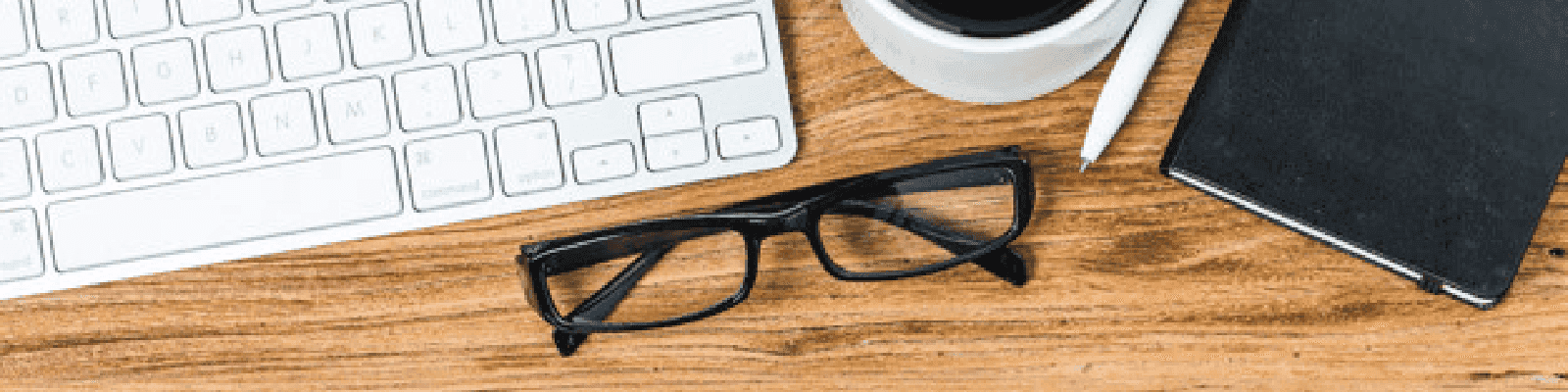
Get in Touch
Manufacturing Equipment Overview
What is manufacturing equipment, exactly? It’s essentially any engineered device which helps you to manufacture your specific items more effectively. There are machining tools, cutting tools, CNC machines, heavy lifting tools, and a wide range of robotics tools currently in use today. But no matter the specific application, many of these tools are driven by similar technologies internally. And when it comes to the essential components which make manufacturing equipment go, the AES team are experts when it comes to repairs and refurbishment.
Here’s a list of examples of equipment and components we’ve repaired and serviced for various manufacturing clients:
- Servo Drive
- Touchscreen
- Stepper Motor
- Electric Motor
- Light Curtain
- Hydraulic Valve
- Hydraulic Motor
- Hydraulic Cylinder
- Hydraulic Pump
- Spindle Motor
- Stepper Motor
- Pump Motor
- Crane Motor
- Hoist Motor
- Brake Coil
- Gearbox
- Gear Reducer
- Valve
- Uninterruptible Power Supply (UPS)
- Transducer
- Servo Motor
- Power Supply
- Operator Interface
- Relay
- Programmable Logic Controller (PLC)
- Monitor
- I/O Module
- Inverter
- Encoder
- Timer
- Counter
- Contactor
- CNC Control
- Circuit Breaker
- Amplifier
- Control Modules
- Printed Circuit Board (PCB)
- AC/DC Drive
- AC/DC Motor
- Industrial Printer
- Control Panels
- Vacuum Pumps
What Are Some Common Issues with Manufacturing Devices & Equipment?
Just as any other type of electronic or mechanical equipment can eventually break down, the same holds true for manufacturing equipment as well. And whenever that happens, your entire production assembly system could come to a grinding halt until the necessary issues are addressed. Here are some of the more common issues we see in our restoration of manufacturing equipment at AES:
Improper maintenance
Inadequate maintenance, or a simple lack of maintenance, can result in a variety of machine issues and equipment breakdowns. Without a regular schedule of maintenance in place – including inspection, testing, cleaning, lubrication, and component adjustment & replacement, many types of manufacturing equipment will experience premature failures.
Operator accidents
In many cases, the fault doesn’t lie with the equipment itself; it actually lies with equipment being handled or operated in an incorrect manner. And in the case of a handheld device, all it takes is an inadvertent drop for sensitive electronics to suffer dislocation or internal damage.
Corrosion issues
Water contamination is a persistent threat, especially in industrial or other high-humidity environments. If rust is able to gain a foothold in your equipment, that can serve to speed the oxidation of oils and other lubricants as well. If this is the case with your manufacturing equipment, then professional service and refurbishment can be your best solution.
Bearing failures
Most manufacturing equipment involves the moving and processing of items from point A to point B. If a bearing or bearings should fail, then so too can the equipment which relies upon those bearings. Premature bearing failure is often caused by the loss of bearing lubricant, or by the intrusion of contaminants. Mechanical defects like misaligned bearings can also lead to premature failures.
Metal fatigue
Another leading reason for industrial machinery failure is metal fatigue. Metal fatigue can occur after several cycles of stress. Metal is typically malleable and resilient, but after sufficient stress produced by temperature extremes or physical load demands, the metal in your equipment can become brittle and start to fracture or break. The best preventative measure is to keep your machinery and internal parts well-lubricated and well-maintained, but even if you do so your equipment may eventually require some refurbishing in any case.
Manufacturing Equipment Repair at AES
Has something gone wrong with your manufacturing equipment? If so, there’s no need to wait – you don’t want to risk having it completely fail whenever you’re in the middle of a production cycle! AES can provide greater peace of mind by taking care of your equipment needs more proactively:
Receipt, Evaluation, & Quote Generation
Once you send your manufacturing equipment to AES, we’ll conduct a thorough evaluation of your items, and will then generate a quote describing what repair & refurbishment work your equipment needs. We’ll make a complete diagnosis of any underlying internal issues, and then we’ll communicate exactly what will be needed to restore your equipment to a like-new condition. It’s always our goal to get you a repair quote within 48 hours of item receipt.
Testing, Repairs, & Retesting
After you officially approve the repair order, we’ll get it right on our technician team’s schedule, and then we’ll get down to business! We’ll troubleshoot your manufacturing equipment – along with all internal components – including providing testing under full-load conditions. We’ll then be able to provide whatever repairs or refurbishment are needed. But that’s not all. We’ll then retest your equipment under realistic manufacturing conditions to make sure that everything is really ready-to-go!
Cleaning & Final Preparations
You might thing we’re finished at that point, but we’re not. At AES we recognize that sensitive manufacturing equipment will work better – and also last longer – whenever it’s properly cleaned and maintained. We’ll remove all oil, dust, contaminants, & residual moisture, and also make sure everything is properly lubricated.
Quality Assurance Measures & Return Shipping
Before we put our seal of approval on your manufacturing equipment, we’ll conduct a final round of quality assurance measures. Once those are completed to our standards, we’ll carefully prepare your equipment for return shipping, including using proper packaging to keep your items in good shape during their journey back to you.
Why Choose AES for Your Manufacturing Equipment Repairs?
AES was founded in 1992, and we’ve always endeavored to provide effective, affordable equipment repairs for all of our clients – commercial, retail, industrial, medical, government, AND manufacturing partners. We’re proud to be able to serve your needs, and to be able to do it in a way that sets us apart:
Efficient Turnaround
A quality manufacturing equipment repair naturally requires a certain amount of time in order to complete correctly, but our team is well-trained and well-equipped to get it done for you fast, too! AES provides a quick standard turnaround time of 8-10 business days for most repairs, but we can also put a RUSH of 1-3 business days on your order, should your desired turnaround time be particularly sensitive. Just let us know what you need, and we’ll work hard to make it happen for you!
QUALITY is Really One of Our Best Qualities
At AES, we understand that some others may see our approach to be “old-fashioned,” but that’s alright with us. Essentially, we’re not willing to cut corners whenever it comes to doing the job right for you. Nobody beats our quality of service, and we maintain the same high standards of quality for every repair, for every client, every single time. We’ve successfully repaired all sorts of electronic and mechanical equipment for our manufacturing clients, and we’d be honored to serve your equipment needs, as well.
A Team of True Professionals
We know we can take care of you the right way. How do we know? It’s because we’ve been doing this for nearly three decades at AES! Our repair technicians are very experienced and knowledgeable – there’s really not a better team in the business! At the same time, we’re also intentional about providing regular training opportunities for our technician team, so that we can make sure to be in the best position to provide exactly what you need to take full advantage of your equipment.
An Effective AND Cost-Effective Solution
Why pay to replace an expensive piece of manufacturing equipment, when all that really may be required is some timely repair, service, and maintenance? AES can get your manufacturing equipment back up & running, plus we’ll restore it to like-new (or even better-than-new) condition! Whenever you choose to make AES your equipment repair partner, you’ll be saving money, you’ll get your equipment back faster, and you’ll also be kept from having to experience many unpleasant and unnecessary headaches.
The Best Repair Warranty Around!
And here’s one more thing to keep in mind about AES. Many other commercial repair providers will settle for offering you a 90-day workmanship warranty. In other words, they’re only willing to guarantee their work for a measly 3 months! At AES, we believe in going the extra mile for you. We stand behind the quality of our repair workmanship, and actually back it with a full 24-Month Limited Warranty. If a problem arises during the stated warranty period, which ends up being a workmanship issue, we’ll be happy to provide a follow-up service for you at NO additional cost! We’re serious about earning your trust.
Connect with AES for Your Manufacturing Equipment Repair Needs
Ready to get all your manufacturing equipment back online and producing for you the way you need and have come to expect? We’re here to make that happen; AES has your needs covered! Reach out today at (866) 386-1001, and let’s get started on your best repair solution! We’re here to take care of you!
Latest Articles & Videos on Electronics Repairs
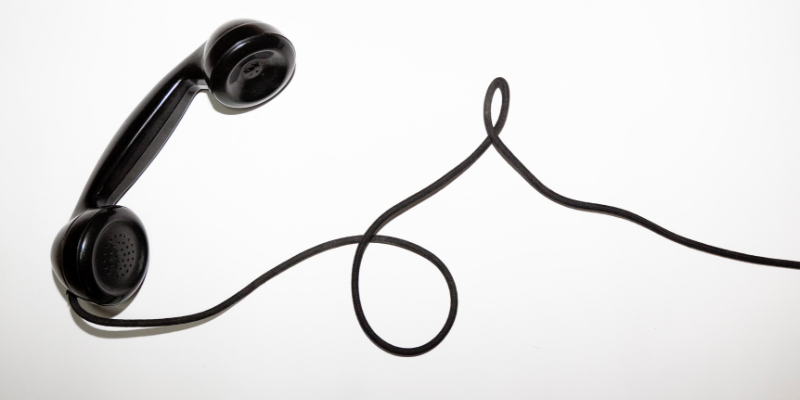
