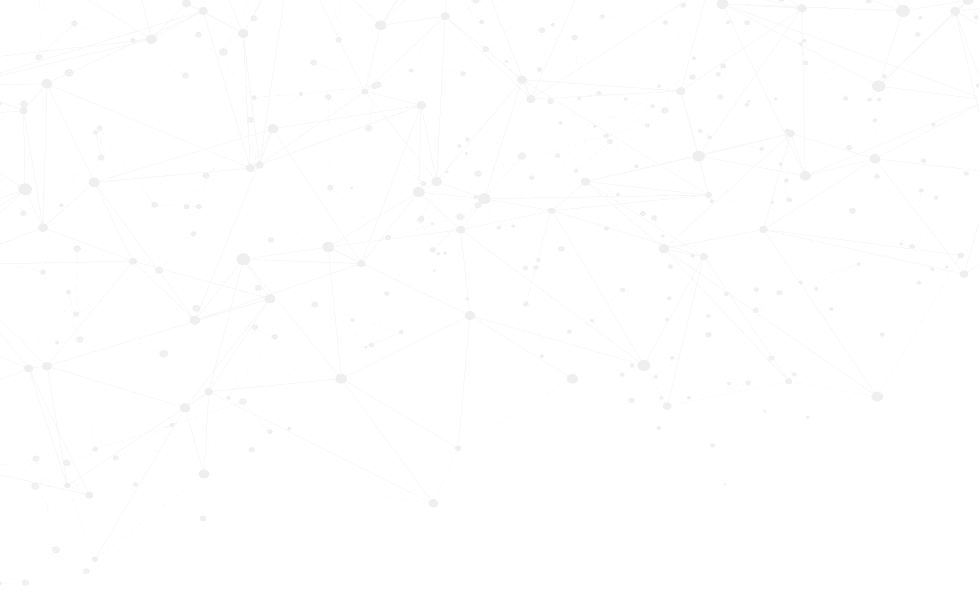
Operator Interface Repair Services
If your business operates within the manufacturing or production space, you probably rely upon some heavy-duty electrical and mechanical equipment for improved productivity, reliability, and efficiency. But no matter how computerized or automated your system is, it still requires some level of human monitoring through an operator interface. But what happens when there’s a problem with your operator interface? Just call the experts at AES!
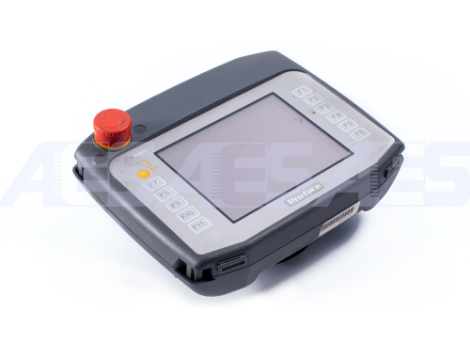
Quickly Search for an Electronic Equipment you are looking for:
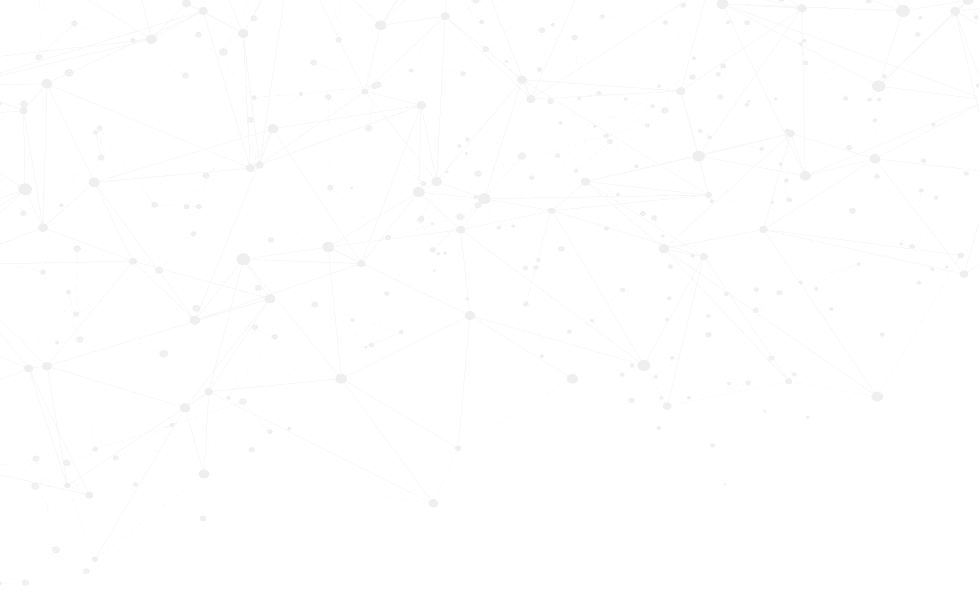
Request a Quote
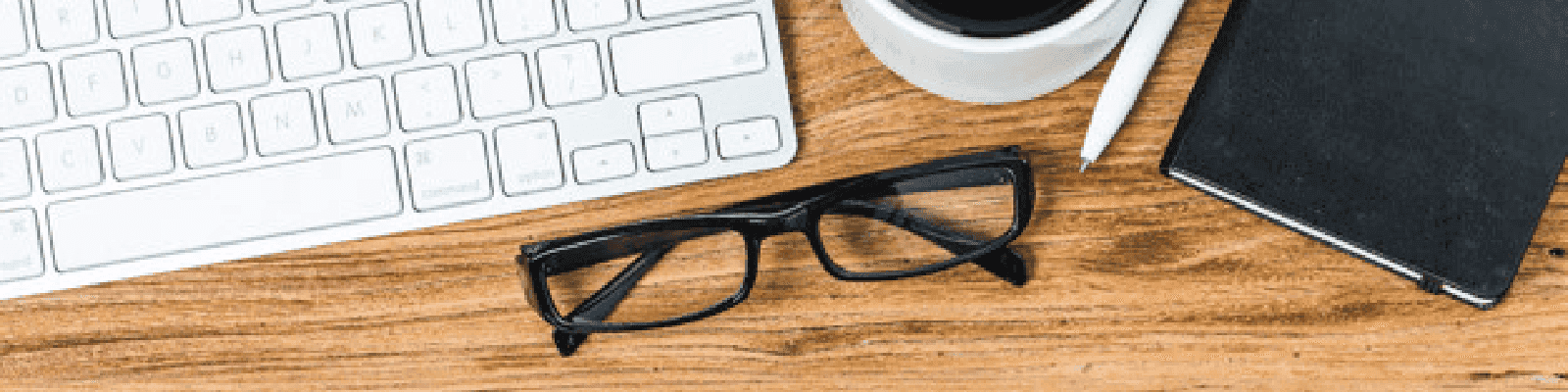
Get in Touch
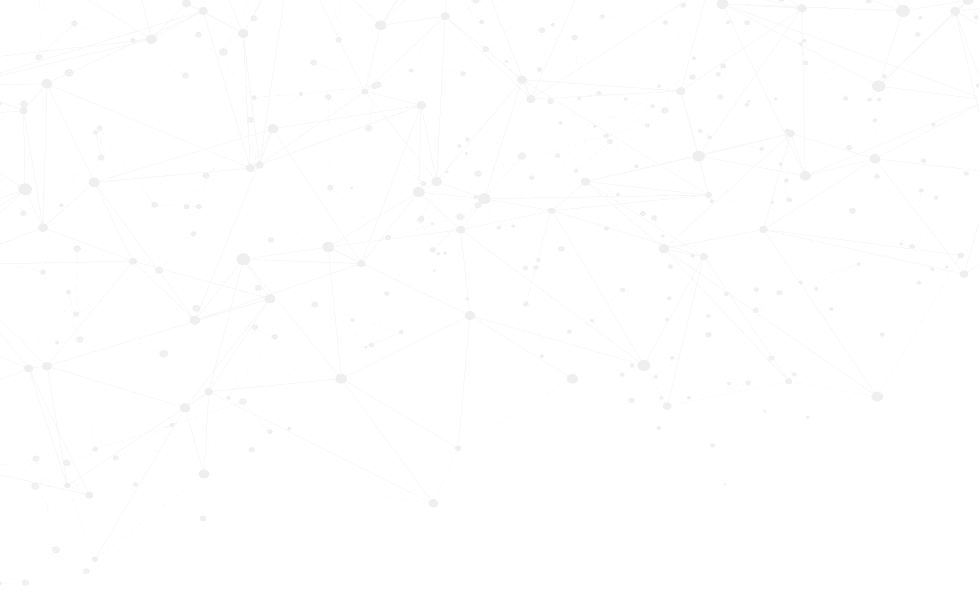
Get started with our simple, proven AES Repair Process
Once we have received your item for repair, we will receive the item in our system.
1Our quoting specialists will evaluate your item and determine the parts and labor necessary to complete the repair.
2Following your approval, we will get to work on your repair. One of our repair technicians will troubleshoot the problem(s) with the item.
3To ensure the highest level of quality throughout the repair process, we comply with ISO 9001:2015 Certified QMS standards, and an ESD program.
4Once the repair is complete, we safely package your item and prepare the item for delivery or shipment.
5Our Partners and Brands We Repair
All product names, trademarks, brands and logos used on this site are the property of their respective owners. The depiction, description or sale of products featuring these names, trademarks, brands and logos is for identification purposes only and is not intended to indicate any affiliation with or authorization by any rights holder.
What Is an Operator Interface, & How Does It Work?
An operator interface can go by many names, including human machine interface (HMI), industrial monitor, or touchscreen panel. In many cases, the name of a particular manufacturer or product like PanelView or PanelMate is used in a generic way to describe any type of operator interface. This shouldn’t come as too much of a surprise, since most people in North America refer to all types of facial tissue as Kleenex, and also call any type of adhesive bandage a Band-Aid.
No matter what you call them, though, operator interface terminals serve some very important functions for proper monitoring and operation of your machinery – not to mention proper supervision of your entire production process. Almost all modern HMI units feature an easy-to-read screen and/or set of visual indicators. These industrial monitors allow you to follow several crucial metrics, and also provide you with both visual and audible alarms whenever there’s a special issue which requires immediate attention. They often usually include some simple controls you can use to help tweak and improve the functionality of your connected machines.
Common Failures with Human Machine Interfaces
As is true with any multifunctional electronic component, an HMI unit is a complex piece of monitoring equipment which can develop some issues over time. This is particularly true if you operate in a facility which includes some harsh conditions. Here are some typical problem areas that may arise:
Touchscreen damage
A touchscreen-equipped operator interface is a very sensitive piece of equipment. While it’s engineered to be resilient in the face of an industrial environment, physical damage is still possible through accidental or improper usage. Touchscreens can also become worn over time through the daily wear-and-tear of regular use.
Power supply issue
Power supplies can become worn down, inefficient, or problematic in any type of electrical equipment over time, and an operator interface is no exception to that rule. In some cases, the power supply itself can be repaired; in other cases, the power supply component will simply need to be replaced.
Lamp failure, or other screen damage
Indicator lamps can eventually fail to light up when you need them. And touchscreens aren’t the only types of screens which require service and attention from time to time. If your screen becomes damaged, or has simply gone dim, fuzzy, or has some dead pixels, the team at AES can help! No matter what type of screen you have – CRT, LCD, LED, or plasma – we have the parts, tools, and know-how to get your industrial monitor, along with any indicator lamps, up and running again!
Battery issues
Many HMI units don’t just have an external power source, they’re also tied to an internal battery as well. An issue with one of your HMI batteries could lead to parameter loss, or in worse cases, a complete program loss.
Contamination
Contamination is a major cause of early life failure in practically all types of electronic equipment. There are many potential sources of contamination for an operator interface, particularly in manufacturing, production, or other industrial environments. There’s an old rule of thumb in the electronic equipment repair business: a dirty or contaminated unit will eventually fail!
Bezel or housing damage
If your operator interface or housing becomes damaged, it can compromise the integrity of the entire unit if not addressed promptly. The AES team will work to repair your bezel or housing; if that proves to be infeasible, we can also fabricate a new one for you.
Indicators That It’s Time to Call AES About Your HMI
One thing to be appreciated about an HMI is that it usually shows you some signs of issues which need addressing before it fails completely. Once these warning signs appear, it’s wise to go ahead and take action before a failed HMI leads to critical downtime for your production process.
Some signs that your HMI is beginning to fail:
- Monitor screen has become faded, dim, or hard to read
- Touchscreen has become less responsive, or has developed some completely unresponsive dead spots
- Screen is obscured with persistent horizontal or vertical lines
- Flickering screen
- HMI screen and/or housing is visibly damaged or broken
- Cable fittings won’t stay tight
- Key presses have become sticky, sluggish, or unresponsive
- Unit won’t start up on the first try
Some Things AES Can Do to Repair Your Operator Interface
Proactive, effective operator interface repairs in partnership with AES can be the perfect solution for a unit that’s become unresponsive or displaying some signs that it needs a little TLC. Sure, you could just choose to replace your older operator interface with a newer model, but that solution can present some unique challenges, too. The new interface might not fit perfectly into the hole where the old interface was. Just as importantly, you may have trouble porting the program from the old operator interface to the new operator interface.
For these and other reasons, choosing to partner with AES for repairs may be the best way to give your old unit new life. Here are just a few of the services we can provide:
- Repair or replace a damaged touchscreen
- Repair or replace a damaged, scratched, or broken monitor screen
- Repair or replace a damaged or scratched or overlay
- Repair or replace dimmed or faded backlights or other indicators
- Re-establish operator interface functionality
- Effectively coordinate with programmable logic control (PLC) systems
The AES Advantage for Operator Interface Repairs
At AES, we’ve performed effective repairs on operator interface and human machine interfaces – along with every other major category of industrial electronic equipment – since 1992! We understand that every successful repair contributes to your company’s ultimate success; that’s why we’re here! Here are few features which set AES apart:
Fast Turnaround
At AES, we know you want your equipment repaired and restored as quickly as possible. That’s what we do! A quality electronic component repair does require some time and attention in order to be performed correctly, but the good news is that our team knows how to work both smarter and harder! We offer a standard turnaround time of 8-12 business days, but if you need your equipment sooner, you can place a RUSH on your order. We’ll do our best to meet your time requirements!
Quality Repairs
Some may think of us as old-fashioned, but that’s alright. AES still believes that if it isn’t worth doing right, it really isn’t worth doing at all. We provide the right repair solution for you the first time, and every other time, too! Our full-load testing process ensures that we’re able to diagnose and correctly repair any performance opportunities or other issues that may need addressing. You can trust that we’ll do what we say we can do!
Experienced Repair Technicians
At AES, we’re confident that there’s no better industrial electronics repair team in the business. Why are we so confident? Because our team of technicians possesses literally decades of on-the-job experience; we know what we’re doing! Plus, we invest in regular training opportunities to improve our team’s skills, which translates to an even better ability to serve your needs, both now and in the future!
A Better, More Cost-Effective Solution
Why pay to replace an operator interface or other expensive piece of electronic equipment, when AES can repair it and get it back to you quickly, for less cost? We’re here to benefit your company’s bottom line! Not only can we get your equipment back up and running again, we can also save you some valuable time, money, and potential frustration.
The Best Warranty in the Business!
And here’s one more solid reason to entrust AES with your industrial repairs. We believe in the quality of our work to the point that we stand behind it with a 24-Month Limited Warranty for ALL REPAIRS! What does that mean? If a problem should arise with your equipment during those 24 months, which is deemed to be a repair workmanship issue, we’ll provide follow-up repair service at NO extra charge! How’s that for exceptional service?
Ready to get your operator interface, human machine interface (HMI), or other essential components back online and working up to its real potential? AES has you covered! Reach out to our qualified team today at (866) 386-1001!