Common PLC Faults and Troubleshooting Procedures
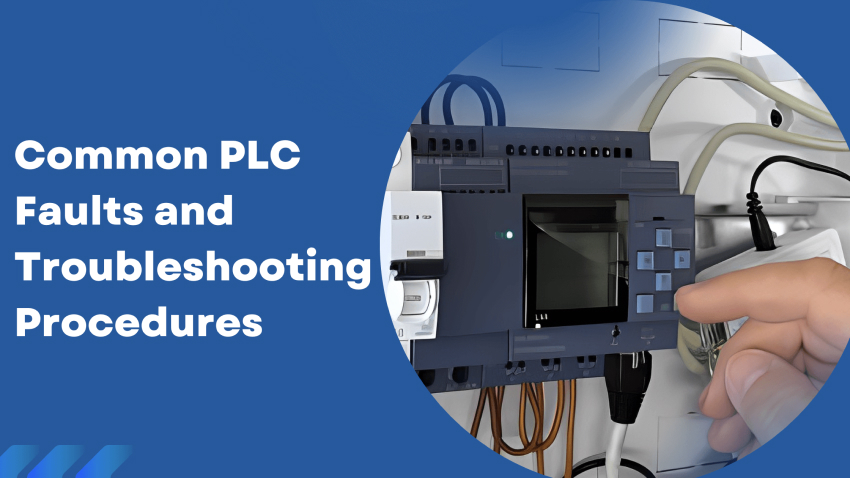
PLCs and Your Business
Programmable Logic Controllers (PLCs) are indispensable devices in the world of automation and industrial control systems. They serve as the brains behind the operation of various machines and processes and keep automated equipment running smoothly. While PLCs are known for their robust nature, like all electronic devices, they’re not immune to wear and tear or occasional malfunctions.
In this blog, we’ll explore these crucial components, show you some of the most common issues with them, and sound troubleshooting advice if you need to perform repairs. If you’re having issues with your automated machinery, the following information might be helpful!
Reasons Why PLC Systems Fail
PLC systems are integral components of many industrial machines, and their failure can be catastrophic in terms of production. Let’s take a look at some of the most common PLC faults:
1. Electrical Failures
Electrical issues can stem from power surges, voltage fluctuations, or short circuits. These can damage the PLC’s internal components, leading to malfunctions. Regular electrical maintenance and surge protection can mitigate these risks.
2. Environmental Factors
PLCs are often exposed to harsh industrial environments, including extreme temperatures, humidity, dust, and corrosive substances. Over time, these factors can take a toll on the system’s hardware, causing failures. Routine PLC repair and maintenance, including cleaning and protection measures, are essential for minimizing the impact of environmental stressors.
3. Software Glitches
PLCs rely on software programs to execute tasks. Programming errors, software corruption, or incompatibilities can lead to system failures. Regular updates and diligent programming practices can help prevent these issues.
4. Component Wear and Tear
Over time, the mechanical components of a PLC, such as fans, connectors, and cooling systems, can wear out. This can result in overheating, electrical issues, and reduced performance. Scheduled PLC repair and maintenance can identify and replace worn-out components.
5. External Interference
Electromagnetic interference (EMI) or radio frequency interference (RFI) from nearby equipment or electrical sources can disrupt the operation of a PLC. Shielding, proper grounding, and isolation techniques can help mitigate these external interferences.
6. Operator Error
Human error, such as incorrect data input, accidental program modifications, or improper handling of the system, can lead to PLC failures. Adequate training and stringent access controls can minimize this risk.
Signs of Impending PLC Failure
Recognizing the symptoms of a potentially failing PLC control module is important in addressing issues promptly and efficiently. Here are some common signs to be aware of that might indicate an upcoming failure:
1. Input/Output Modules and Field Devices
A failing PLC control module may cause issues with input and output modules or field devices. Symptoms may include erratic readings, malfunctioning sensors, or actuators that fail to respond as expected.
2. Ground Integrity
Ground integrity problems can result in electrical noise and interference. Look out for erratic readings, unpredictable behavior, or voltage fluctuations in the control system, which can indicate ground-related issues.
3. Power Supply Failure
If the power supply to the PLC control module is compromised, the system may become unstable or fail to power on. This can result in intermittent failures or complete system shutdowns.
4. Electrical Noise Interference
Electrical noise interference can disrupt the normal operation of a PLC, causing incorrect readings and erratic behavior. This interference may be caused by nearby equipment or electrical sources.
5. Loss of Network Communication
A failing PLC control module might lose its ability to communicate over the network. Network communication errors, dropped connections, or missing data are telltale signs of this issue.
6. Excessive Heat
Overheating is a common symptom of a failing PLC control module. High temperatures can lead to component damage, affecting the system’s overall performance and lifespan.
7. Conflict with Other Components
Incompatibility or conflicts with other components within the control system can cause the PLC to operate erratically. This might manifest as errors, unpredictable behavior, or even system crashes.
8. Corrupted Memory
Memory corruption within the PLC control module can result in unpredictable outcomes and unreliable operation. Symptoms can include program errors, data loss, or system crashes.
Troubleshooting PLC Failures
Now that we’ve examined some of the most common faults in PLC control systems, let’s look at the most efficient ways to handle them:
1. Troubleshoot Ground Loops
Ground loops are common in PLC failures, leading to electrical noise and interference. To address this issue, verify the ground integrity of your system. Ensure all components are correctly grounded, and there are no unintended ground paths. You may need to isolate sensitive components or use isolation transformers to minimize ground loop effects.
2. Check PLC Indicators
PLC control modules often include status indicators that provide valuable information about the system’s health. Examine these indicators to identify any error codes or fault messages. Consult the PLC’s documentation to interpret the indicators correctly. This can help pinpoint the source of the problem, and allow you to make quick PLC repairs.
3. Troubleshoot PLC Inputs
Erratic readings or unresponsive sensors are common issues with failing PLCs. Start by checking the input devices, such as sensors and switches. Ensure they are correctly wired and functioning as expected. Testing these devices with a multimeter can help identify faulty input components.
4. Troubleshoot PLC Outputs
If actuators, relays, or other output devices fail to respond as they should, investigate the output side of the PLC. Examine the output devices for faults, damaged wiring, or loose connections. It’s also crucial to verify that the PLC program logic for controlling these outputs is error-free.
5. Troubleshoot the CPU
The CPU is the brain of the PLC, and problems with the central processing unit can lead to system-wide issues. Examine the CPU for overheating, loose connections, or damaged components. If you suspect a problem with the CPU, it may be necessary to consult a PLC repair and maintenance service provider to perform a thorough diagnostic and repair.
AES is Your Premier Choice for Any Electronic, Hydraulic, or Mechanical Repairs
AES takes pride in taking on challenges and bringing fast, effective solutions to a wide variety of industrial repairs. Need PLC repair and maintenance services? We can help. Have issues with your hydraulic components? We do that, too!
No matter the field, we’ll provide you with a PLC repair service you can count on. Call AES today at 866-386-1001 and speak with one of our experts about finding a solution to your industrial tech woes.
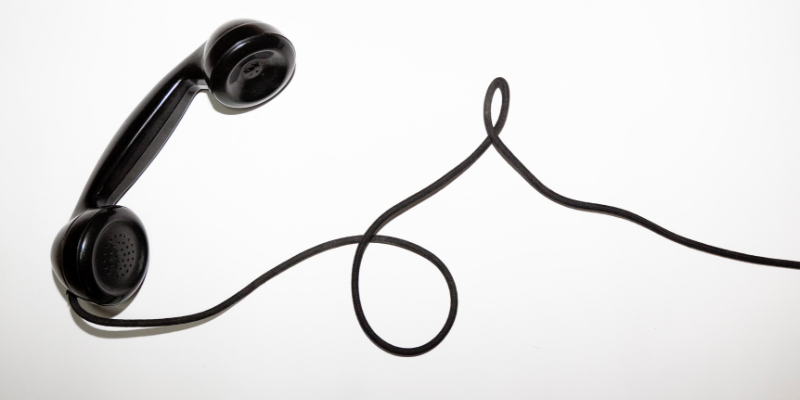
