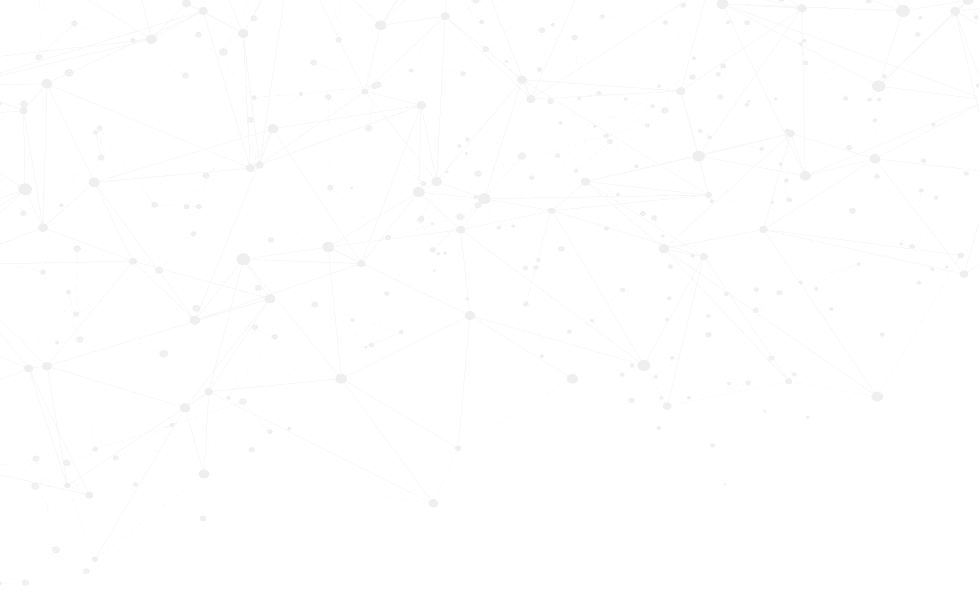
Programmable Logic Controller Service – PLC Repair
If your business involves manufacturing, fabrication, or some type of production, chances are very good that you make use of automated machinery operated by a programmable logic controller (PLC). If there’s an issue with a PLC, then your machine could be rendered useless. PLC replacement isn’t the only option; AES can come alongside to provide effective PLC repair services for less!
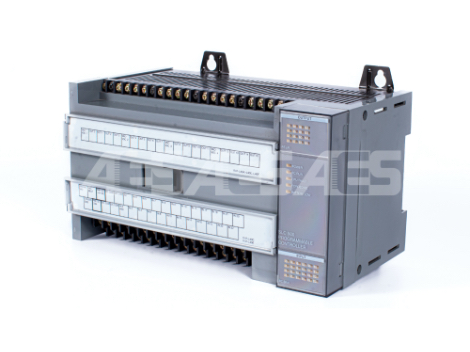
Quickly Search for an Electronic Equipment you are looking for:
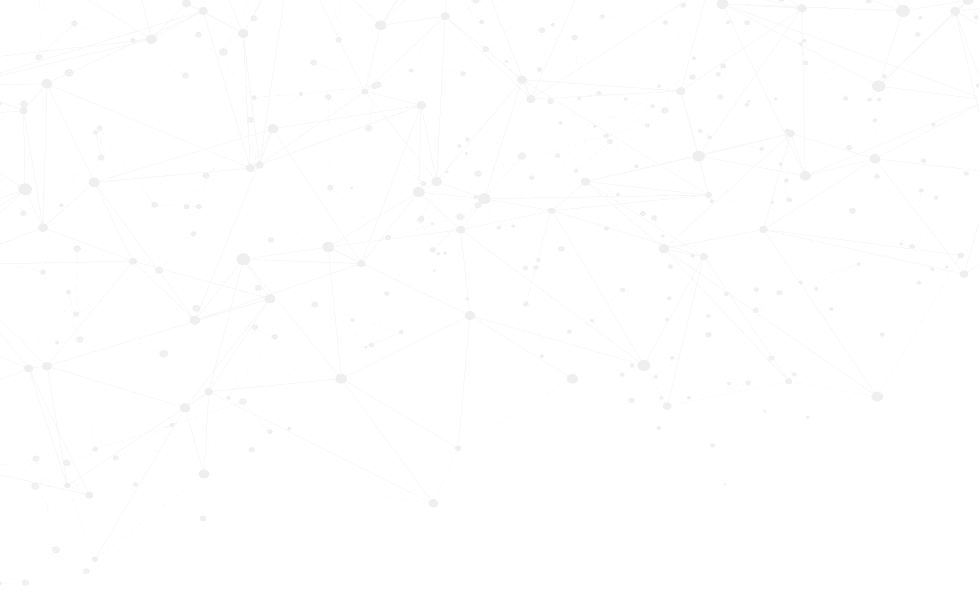
Request a Quote
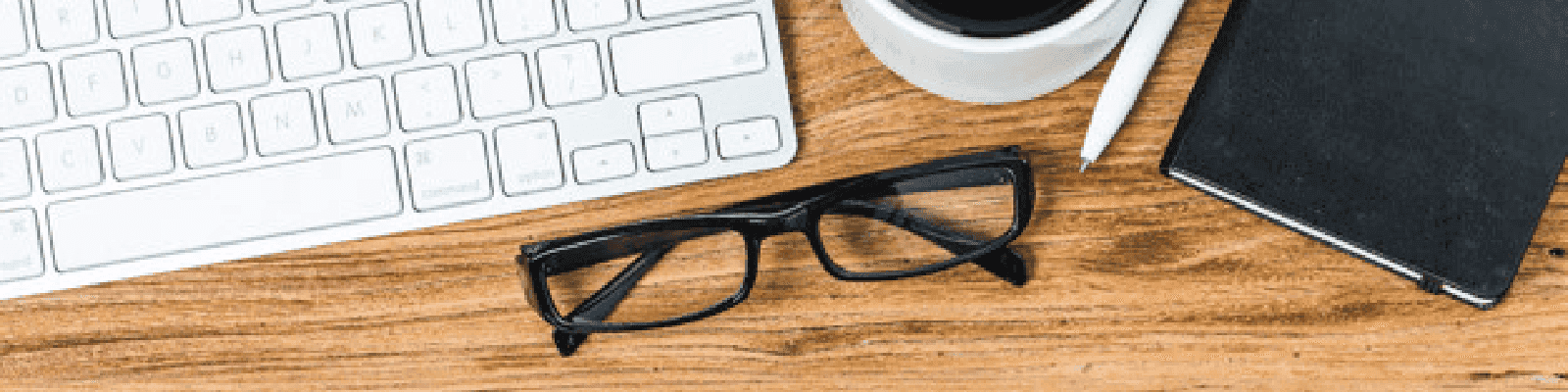
Get in Touch
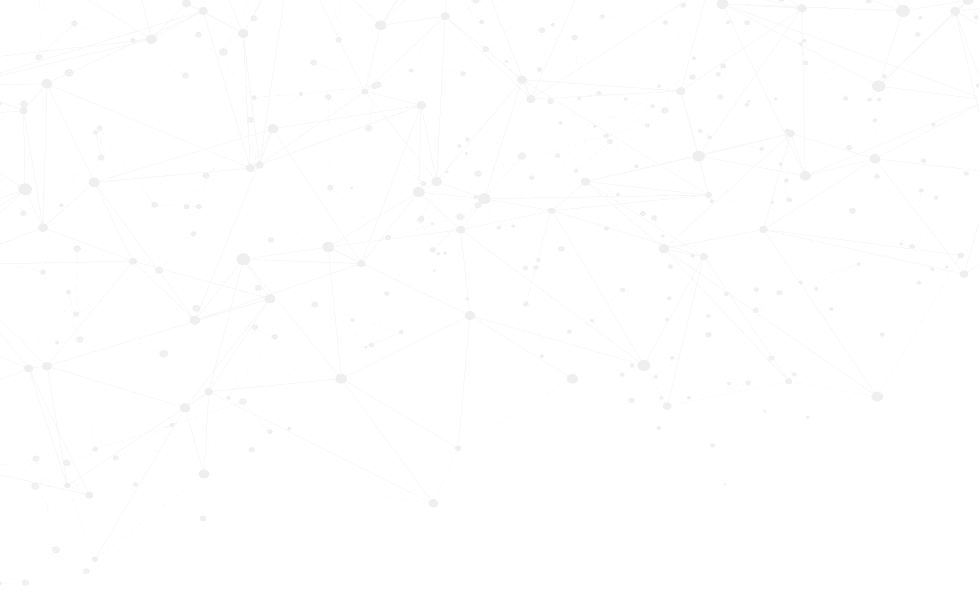
Get started with our simple, proven AES Repair Process
Once we have received your item for repair, we will receive the item in our system.
1Our quoting specialists will evaluate your item and determine the parts and labor necessary to complete the repair.
2Following your approval, we will get to work on your repair. One of our repair technicians will troubleshoot the problem(s) with the item.
3To ensure the highest level of quality throughout the repair process, we comply with ISO 9001:2015 Certified QMS standards, and an ESD program.
4Once the repair is complete, we safely package your item and prepare the item for delivery or shipment.
5Our Partners and Brands We Repair
All product names, trademarks, brands and logos used on this site are the property of their respective owners. The depiction, description or sale of products featuring these names, trademarks, brands and logos is for identification purposes only and is not intended to indicate any affiliation with or authorization by any rights holder.
What Does a PLC Do, & How Does It Work?
A programmable logic controller (typically just abbreviated as PLC for short) is a basic “brain” for governing your industrial or mechanical equipment. It involves functions like motion control, relay control, and output process control. A PLC is designed to help facilitate the smooth operation of automated machinery, motors, tools, and devices within set parameters.
How does a PLC work, exactly? Based upon the inputs it receives, it sends out corresponding outputs to its connected devices in a fast, efficient, automated fashion. The flow goes like this: the PLC receives an input, it sends an associated output according to its programming, and this output then directs a connected device (or devices) to perform a specified function. PLCs have many advantages over non-programmable controllers, including greater reliability, more flexibility in application, and better automation of essential processes.
The PLC Repair Process with AES
Programmable logic controllers are really essential to many modern industrial operations and applications, thanks to their ability to help various electronic devices and machines to communicate and work together in tandem. Unfortunately, a problem with one of your PLCs can throw a wrench into the whole process. The good news is that AES has a proven process for diagnosing and repairing PLCs! Once you send your component to us, here’s an overview of the procedure we’ll follow to get your equipment back up and running again:
*Free evaluation & repair order confirmation: The first thing we’ll do is conduct a FREE, thorough analysis of your PLC to pinpoint any problem areas. We’ll then send you a quote detailing what will be needed in order to provide you with an effective repair. Once you confirm the repair order, we’ll put your PLC on our repair schedule, and our team will get to work!
*Inspection: We’ll power up your device and check all of its inputs, outputs, and physical connectors.
*Individual component repair & replacement: We’ll examine each component of your system, and make necessary component repairs wherever feasible. Components with particularly high failure rates like relays, capacitors, and isolators may just need to be replaced. Thankfully, we maintain an extensive inventory of both common and hard-to-find parts, so our team can service practically any PLC, regardless of manufacturer or model.
*Run a test program: After we inspect, repair, and replace all needed elements, we’ll run a test program on your PLC. This test is designed to make sure your central processing unit (CPU) and the logic system are functioning correctly.
*Further testing: We’ll also test other essential areas, like the battery, circuitry, and ladder logic. We’re intentional about testing every aspect of your PLC under normal load conditions, to ensure that everything is now functioning properly before we ever label your repair as completed.
*Cleaning: The repair itself may now be completed, but we’re not finished yet. We’ll also give a thorough cleaning of the entire unit, and then we’ll test it one more time to make sure everything is good-to-go. Our intent is to return your PLC in as close to new condition as possible!
*Packaging: Now that our repair process is complete, we’ll carefully pack your PLC and prepare it for prompt shipment back to you!
Why Choose AES for Your PLC Repair Service?
There’s no need to pay to replace an expensive PLC when our team can provide needed repairs for less! One thing our clients really appreciate about AES is the way they can count on us to meet their equipment service needs, while also saving them time and money in the process! Here’s a summary of what sets AES apart:
Quick Turnaround
A quality PLC repair does take time, and really isn’t complete without proper load testing. Thankfully, the AES team doesn’t just know how to do the job right, we know how to get it done FAST, too! We offer a fast standard turnaround time of 8-10 business days for most projects, and we can also provide a RUSH turnaround time of 1-3 business days, if that’s what you require!
Quality Repairs
At AES, we’re committed to providing the highest possible quality of repair services for every single project, for every client, every time. We’ve successfully repaired tons of PLCs over the years, and we can help you with yours, too!
Experienced, Trained Repair Service Team
We’re confident in our abilities to serve your needs at AES. Why are we so confident? Our team of repair technicians possesses decades and decades of combined experience, and we’ve seen a thing or two when it comes to industrial electronic equipment. Of course, we don’t just rest in our on-the-job experience, either. We’re also intentional about investing in regular training opportunities that benefit our team, and which ultimately benefit our ability to serve you even better!
Best Warranty in the Industry!
Most repair companies offer some type of warranty, but our warranty is simply the best in the business! We stand behind everything we do by offering a full 24-Month Limited Warranty for ALL REPAIRS! If a problem arises during that time frame which is deemed to be a workmanship issue, AES will be happy to provide follow-up repair service at no additional cost to you!
Nobody Takes Better Care of You Than We Do!
AES is your go-to source for effective PLC repair, but that’s not all we do. You should really just think of us as your “one-stop-shop” for any and all industrial electronic equipment repair needs…because that’s exactly what we are! Our team is trained & equipped to work on practically ANY type of equipment, but even if we come across something we haven’t seen before, we’re equipped for that too. Our in-house engineers can even help us to create an innovative, effective repair solution for you. In other words, AES has you covered!
Ready to get your PLC back online and running at full potential? AES is here to take care of you – connect with us today at (866) 386-1001!