Servo motors and drives are crucial components for keeping your industrial equipment humming along and doing its job. But what happens when you have a problem with your servo drive or motor? Sure you could pay to replace it, OR you can partner with the AES team of trained experts to provide you with effective servo testing, repair, & rebuilding services for less!
Our Offerings in Servo Repairs
Servo drives are essential components for keeping many industrial equipment applications humming along and providing the results you need for your business. But what happens when there’s a problem with your servo drive? Sure, you could simply replace it, but that really might not be your best option. Partner with the AES team of trained experts and receive effective servo testing, repair, & rebuilding for less!

Servo motors are a widely-used source of controlled, reliable mechanical power for a wide range of specialized industrial and commercial applications. But if your servo motor stops rotating, your machinery and devices stop working. Why replace it, when skilled service & repair can be a much better option? Partner with the AES team of trained experts for effective servo testing, repair, rebuilding, and more!
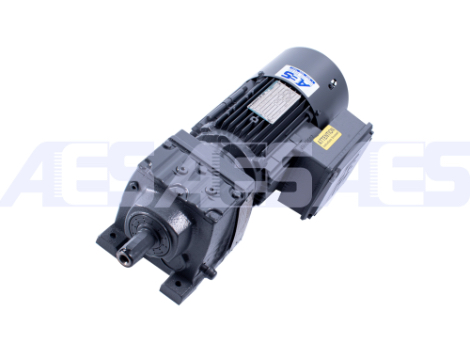
Servo Equipment


Industries We Serve in Servos!
Our Partners and Brands We Repair
All product names, trademarks, brands and logos used on this site are the property of their respective owners. The depiction, description or sale of products featuring these names, trademarks, brands and logos is for identification purposes only and is not intended to indicate any affiliation with or authorization by any rights holder.
Some Common Causes for Servo Motor Problems
If you use servo motors frequently, it’s a good idea to be familiar with common problems that can arise. Learning more about how a servo works (and how it can malfunction) will help you with diagnosing issues. You’ll also have a better idea of when to seek out professional repair or service.
Improper Installation: Sometimes mistakes occur during the installation of your servo motor or drive, and this can lead to problems. For example, a belt that’s too tight or improperly placed can greatly diminish servo performance.
Damaged Cables: If a cable becomes damaged, that can certainly lead to a servo motor breakdown. Damaged cables are relatively common, and they can also produce some motor-damaging voltage spikes.
Intrusion of Contaminants: Your servo is a sensitive machine, so any intrusion of contaminants like dirt, oil, cutting fluid, or coolant can cause damage to internal components like bearings, windings, and electrical components.
Overloaded or Overworked Motor: Your servo motor is likely to become damaged if it’s overloaded or overworked. You can help prevent this by ensuring appropriately-sized loads and making sure to give your motor enough needed downtime.
Bearing Failures: One of the most common sources of problems with servos are faulty bearings. If you hear screeching or whining, replace those bearings! Otherwise, you can end up with total servo motor failure.
Brake Dust Buildup: A high-pitched squeal can indicate dusty brakes in your servo motor. Brake dust can spread internally and compromise other important systems. Regular servo maintenance can help to prevent these issues.
Mechanical Binding or Circuit Overloads: Mechanical binding and/or circuit overloads can make your servo motor run hot. If you suspect that your motor is running hot, get it checked out right away to avoid permanent damage.
Faulty Power Supply or Drive: Sometimes a servo can have an inadequate power supply or a bad drive. The motor itself may be fine, but the failures of these items could cause the system to malfunction.
Positioning Errors: A positioning error can also cause problems for your servo motor, resulting in some buzzing or “chatter.” A proactive positioning adjustment can prevent a lot of headaches down the road!
Improper Setup or Parameter Issues: Setup issues and parameter losses can cause similar chattering issues to positioning errors. Check for this by running through the motor/drive setup procedures. If that doesn’t fix it, seek professional service.
Winding Issues: Problems with a servo’s winding can also make the motor run hot and result in damage. Whether caused by contamination or by an internal short, the winding should receive prompt service.
Electrical Failures: Capacitors, diodes, resistors, resolvers, encoders, and similar electrical components all wear out eventually. As these electronic items degrade, your motor’s performance will also become compromised and require some TLC.
Neglected Servo Maintenance: Neglecting to have your servo motor serviced regularly can result in many of the above-mentioned problems. Scheduling basic servo motor maintenance can help you avoid many more costly repairs.
Expert Servo Electrical and Mechanical Repair from AES
A servo system includes several integrated components, but the two most prominent are the servo drive and the servo motor. Essentially, the servo drive translates incoming command signals into voltage and current needed to power the servo motor. If either component isn’t functioning properly, then the system will have performance issues.
Servo Motor: Servo motors are a kind of electric motor controlled for specific angular rotation. They’re used in closed-loop mechanisms for a variety of purposes. AC and DC motors are some of the most well-known servo motors used regularly in a wide range of smaller-scale devices, but servo motors also have many essential industrial applications. In a larger industrial or commercial setting, it’s important for a servo motor to possess critical positioning and speed sensing capabilities.
How are your servo motors performing for you in your mission-critical business or organizational applications? Have you had a servo motor breakdown? Or does your servo motor need optimizing for maximum performance? AES can take care of you!
Servo Drive: A servo drive could be described as an amplifier of sorts. It receives control signals from a controller, and then escalates the signal to deliver whatever voltage and current are needed for the servo motor to be able to achieve the needed outcome. In terms of industrial and commercial applications, servo drives are utilized for everything from machining, to automation, to robotics and more. Without a properly functioning servo drive, your servo motor could be rendered practically useless.
Is your current servo system broken down or underperforming? It’s possible that your servo motor is actually fine, but your servo drive needs some attention. The expert team at AES is more than capable of getting your servo drive back online!
AES Specializes in Servo Motor and Servo Drive Repairs & Service
When it comes to the professional servo motor and servo drive repair services, no one is better equipped to take care of your needs than the AES team. Our servo specialists collectively possess decades of hands-on technical training coupled with extensive practical repair knowledge and experience. We’ve got you covered!
Load Testing: We’re able to test servo systems at full capacity under load, so we can detect potential issues that others may miss. With our industrial load simulators and monitoring equipment, we’re able to both identify all the factors which are keeping your servos from providing you with maximum performance.
Complete Machine Shop: Thanks to our complete machine shop, we can do more than just identify issues with your servo motors and servo drives. We’re also more than capable of providing solutions to the problems we find with your system.
Remanufacturing: It’s possible that your servo motor or drive could require some remanufacturing or rebuilding in order to achieve optimal performance. That’s not a problem for the AES team!
New & Used Sales: In addition to our respected repair services, we’ve also expanded to include new and used component sales to better meet your needs. So whether your individual needs dictate either rebuilding or replacement of a particular component, AES can take care of you equally well in either circumstance.
Why Partner with AES? Experience the AES Difference!
Sure, there are other companies out there who offer servo repair services… but none of them can take care of your equipment testing, repair, refurbishment, or replacement needs like AES! Here are just a few reasons you should choose to entrust your needs to our dedicated team of specialists:
Comprehensive Service: AES truly is a “one-stop-shop” for all your repair needs. Sure, we repair servos, but we also have dedicated technicians for all sorts of other industrial specialties. We also are proud to employ an in-house team of engineers, as well. In other words, if it needs fixing, our team has all the knowledge and tools to get you back up and running again!
Dedication to Quality: At AES, we believe in doing the job right for you the first time, and every time! Each repair project presents its own set of individual challenges, but that never presents a discouragement to our team. We really thrive on these kinds of challenges! We’ll hang in there and keep working on the problem until we can provide you with the absolute best solution for your needs.
Faster Turnaround Time: A quality servo equipment repair takes time to complete, especially with our extensive testing protocols. But thanks to having a complete team of trained professionals on-site, we don’t just get your job done right, we also get it done faster than our competition. And if you require a time-sensitive solution, then no one’s better equipped to meet your needs than AES! We offer a fast standard turnaround time of 8-10 business days for most projects, and we can also provide a RUSH turnaround time of 1-3 business days, if that’s what your needs require!
Trained, Experienced, & Ready to Serve: Our team knows what we’re doing! Many of our repair technicians possess 20, 30 or more years of experience in successfully repairing equipment just like yours. But we don’t just rest in that experience. We also provide regular training opportunities so our individual team members can broaden their respective skill sets, in order to better serve your ongoing repair needs.
FREE Evaluations & Competitive Pricing: We offer FREE evaluations and quotes for every repair and service we provide. In other words, we’ll diagnose your problem and explain exactly what your repair solution will involve, before you ever place your AES order. We’re also committed to completing your project with prices that are always competitive and fair. And our personal standard of workmanship is really second to none!
Personalized Customer Service: Some other repair companies make you feel like “just a number,” but that’s NOT how we operate at AES. Each and every customer relationship is important to us. We don’t just see you as a customer or a client; we see you as a real business partner. Once you entrust your business to AES, you’re assigned an individual account manager and account specialist. That way, we’re best able to take care of your needs in both a professional and a personal manner.
Affordable Solutions: Why pay to replace an expensive piece of servo equipment, when our team can repair and refurbish it for MUCH LESS? One of the things our many satisfied clients like best about AES is the way we come alongside to meet your servo equipment needs, while also saving you money at the same time!
Industry’s Best Warranty: And here’s another game-changer when it comes to choosing AES. We believe in the quality of our services and workmanship so much that we provide a 24-Month Limited Warranty for ALL REPAIRS! If a problem arises within that time frame, which is related to the workmanship of AES, we’ll provide any needed follow-up service at no additional cost!
Trust AES for All Your Servo Repair & Service Needs
AES has been providing quality electronic and industrial mechanical repair services since our start in 1992, and we continue to do so today. We’ve also expanded to include the sale of both new and used industrial equipment components from thousands of respected supply vendors, in order to better meet the needs of our many customers. You can trust AES with your servo equipment repairs, and you can also trust us with your other surplus industrial equipment needs, too.
Ready to get the conversation started? Just fill out our Request a Quote form, shoot us an email at sales@aesintl.com, or give us a call at (866) 386-1001. We’ll do our best to provide what you need, when you need it, and we’ll do so with the best customer service in the business! Got an equipment problem that needs fixing? AES is here to help!
Latest Articles & Videos on Servo Repairs
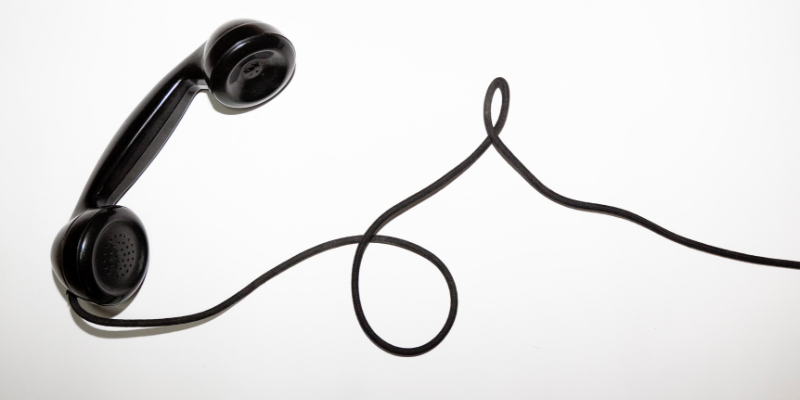
